Fårbo Mekaniska is a long-established machine workshop and production facility in central Sweden. The company has been producing quality components and assemblies for customers in the mining, toolmaking, steel production and machining industry for decades. Thanks to its comprehensive range of machinery and highly qualified employees, the company has earned a reputation for delivering high-quality solutions in the shortest possible time. This is also because the company focuses strongly on technology and productivity. And they have implemented a culture that encourages everyone to make suggestions for improvement.
It all started with an idea
Markus Brännström, consultant for application technology, had one such idea and sought a conversation with Roger Berggren, CEO of the company. What drove Brännström was the question of how the performance of two older machines could be increased. This was because, even though they were already old, they basically still fulfilled all their tasks and, from his point of view, still had countless years of reliable production ahead of them. In view of the constant influx of customer orders, they asked themselves how the spindles could be better utilized.
"We felt that these two machines were running pretty well, but we felt that they could run more often, we just didn't know how much more often," says Brännström. So, while the business continued at its usual pace, they were looking for a monitoring option. Without this, they were certain that they would struggle to find ways to optimize capacity utilization. Modern machine control systems are equipped with proprietary software and a dashboard as standard, enabling transparency and supervision. But older machines lack this technology. However, Fårbo Mekaniska found a solution.
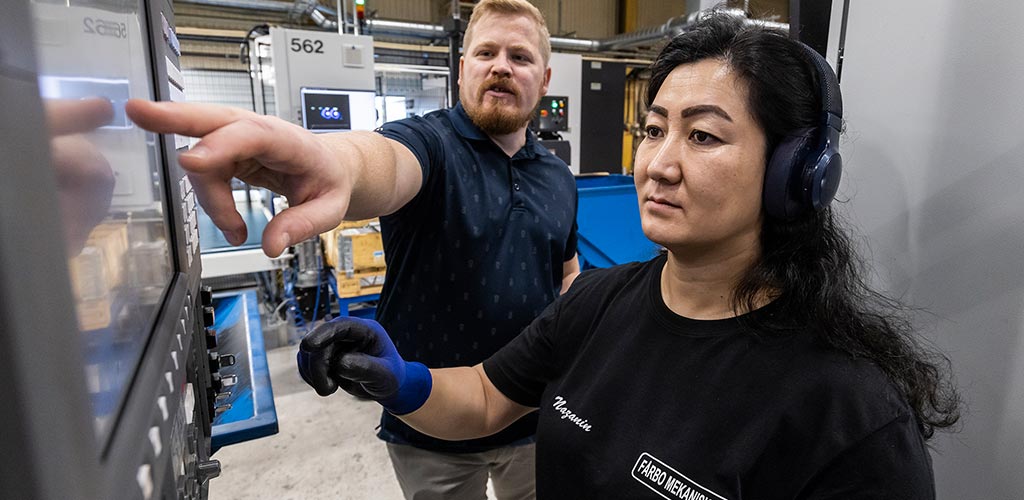
The answer: TDM appCom
One of the two machines is used for deep hole drilling and works with an oil pump motor. "All we can tell from this is whether the machine is running or standing still," says Brännström. But that was a very good start. With the oil pump forwarding the machine's start and stop cycles, Fårbo had the first important information regarding the actual utilization of the machine. The second of these two systems is a special shaft machining center with an older Siemens control system. In this case, Brännström enabled connectivity through an electrical output of the control unit. Here, too, connectivity was made possible by installing a simple relay, which initially provided basic switch-on and switch-off information.
"This was our first step in gaining insights from these two machines," says Fredrik Svensson, Corporate Development Manager at Sandvik. Svensson works closely with Fårbo Mekaniska's productivity and efficiency goals and supports the company with numerous CRIBWISE installations, a solution from Sandvik Tool Flow Solutions. "The big win for Fårbo Mekaniska is to start recording this type of data and then utilize the power of the software and the creativity of the production managers to increase productivity," Svensson continues.
Valid data for optimized capacity utilization
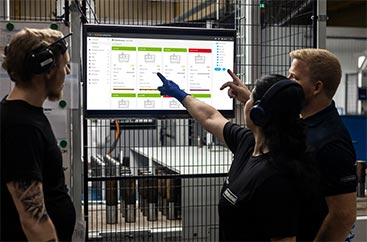
TDM appCom software was introduced at Fårbo Mekaniska, and this was used to also integrate the two older machines into the machining network for the first time. The software has robust functions for recording, evaluating, visualizing and interpreting extensive production and CNC machine data. It therefore offers far more than can be implemented in the two cases. Another advantage: TDM appCom works across all manufacturers and can be used for various CNC control systems and interfaces such as Siemens, Fanuc, Heidenhain, OPC-UA, MT Connect or UMATI.
"The plan is to introduce tablets next to each control panel that can be used to report machine down times," says Brännström. With operator involvement, Fårbo Mekaniska plans to record more information, such as tool breakage, material shortage, waiting for technical assistance or waiting for quality approval, to name just a few. The company is still in the initial phase – the learning and training phase for the system. However, the goal is to identify how much the machines are actually running and then create a plan to increase productivity. Ultimately, Brännström wants to enter the actual efficiency data into the company's ERP system to enable more accurate planning for the future.
Visibility and metrics on the same scale
Most of the equipment used at Fårbo Mekaniska today is state-of-the-art. And, in order to meet growing customer requirements, the company is constantly expanding its production area and investing in additional equipment. More than 56 machines and 25 automated systems from a wide range of manufacturers are currently in use. For many of them, TDM appCom is the only standardized solution.
"One of the biggest simplifications is the presentation of the OEE diagrams. They are all presented in a common form, so things like scaling don't have to be interpreted," says Brännström. This applies regardless of the brand of the machine tool or CNC control or whether the installation takes place in a local network or in the cloud. In the case of Okuma machines, for example, TDM appCom is connected to all machines via the proprietary OSP controller and MT Connect (versions P200 and P300). The solution collects all of the necessary data such as tool number, spindle load, feed rates and speeds. The goal is a weekly check by TDM appCom. And therefore, to determine how long which machine has been running and how capacity utilization can be improved. Although the system is still in its initial stages at Fårbo Mekaniska, it is already providing valuable insights. For Fårbo Mekaniska, the one-solution approach is an important step towards standardizing data and a valuable tool for decision-making.