The SOFLEX PCS production control software ensures long tool lives at the automation experts Liebherr Verzahntechnik, despite the high degree of individualization of the workpieces. It controls the entire manufacturing process and plans the complete workflow on the basis of the data in the ERP system. In combination with the TDM Tool Management, "this enables highly flexible, reliable, and efficient manufacturing around the clock," says Matthias Dodel, CAM Programmer and Production Line System Supervisor at Liebherr.
Replacing outdated software solutions
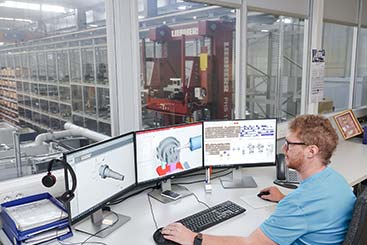
With the decision in favor of an automated milling and turning center, Liebherr was searching for a new tool management solution. This is because the old software was a proprietary standalone solution, which had been specifically tailored to work with our previous CAM software and was therefore not compatible with the new solution." Since the company repeatedly encountered highly satisfied TDM users during its reference visits to numerous CAM manufacturers and, according to Dodel, also within the Liebherr Group, Liebherr took the decision in 2018 to go with the tool management solution offered by TDM Systems.
"TDM is a software with many interfaces that offers us great versatility and freedom, enabling us to implement our digitalization concept efficiently," says Dodel. An automated data flow is enabled in particular by the interfaces of the TDM solution to the ESPRIT CAM system, Soflex manufacturing control system, and the Zoller presetting system.
"Eliminating manual data input reduced the error rate down to zero," comments Dodel. However, Liebherr not only uses TDM in the classic way for tool management, but also as a document management system for the CAM documents, NC programs, or setup instructions. The Tool Crib and Fixture Management Module together cover all tool and fixture requirements of the machining centers.
Direct data access saves time
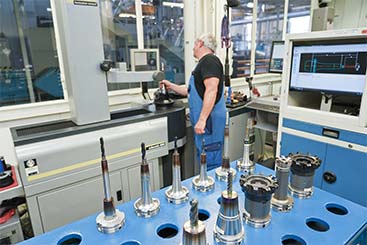
With small series down to a lot size of 1, NC programming can quickly become a bottleneck on the shopfloor. This is not the case at Liebherr. In fact, the company has produced approximately 5000 NC programs within just four years – while operating with the same workforce and also extending its fleet of machines. "In the past, we would have needed ten years for this," says Dodel.
The fact that the NC programmers achieve such excellent efficiency can be attributed to the modules for data and graphic generation, as well as the TDM-ESPRIT CAM interface. After all, this facilitates end-to-end use of the unequivocally defined tool assemblies, also as digital twins for simulation purposes. In addition, manual data input during programming is completely eliminated.
In total, Liebherr manages some 3800 tool assemblies and 7000 fixtures. When the manufacturing control system is planning an order, the tool assemblies required for this are determined. The requirements are then compared against the tools available on the machines and the respective tool lives. If any tools are missing, these are fitted, preset, and measured on the basis of a requirements list from Soflex. Tool changes are performed when necessary or once the respective tool life has expired. This is a fully automatic process. "Without TDM, we simply would not be able to ensure the requisite tool supply – which would then also make automation impossible," concludes Dodel.
Prior to implementation of TDM
- Replacement of the outdated tool management and CAM system, as not designed for automated
production - Implementation of the Liebherr digital concept and redesign of the entire process chain in planning and production with automated, end-to-end flow of data
- 100% tool availability at the machine for automated setup
Process innovation
- More efficient CAM processes: Access to end-to-end data and graphics, as well as defined standard tools for each machine
- Comprehensive networking with the production systems facilitates reliable tool requirement planning for all orders/machines
- Automated tool provision thanks to available lists of requirements and installation instructions
- Wide range of interfaces facilitates a fully end-to-end process chain and tool data support in all shopfloor systems
- Reproducibility is secured through document management and tool lists