Here seafaring finds a home and MAN France sits right in the middle of it all. The journey to the industrial complex between the wharfs and the shipyards - leads through kilometers of port. “Wow! What’s that?” visitors might ask spontaneously at the sight of the objects on the MAN grounds. They are finished engines whose size could rival that of any delivery truck.
MAN’s predecessor company S.E.M.T., the Société d’Etudes de Machines Thermiques, produced diesel engines in Saint-Nazaire under the Pielstick brand name starting in 1946. The company was named after Gustav Pielstick, a German engineer and expert on ship engines. He began his career in 1911 at the MAN plant in Augsburg, Germany, the headquarters of the group that now belongs to Volkswagen.
Pielstick personally met Rudolf Diesel, who died in 1913. He devoted himself mainly to the development of diesel engines for the maritime industry. Starting in 1946, Pielstick connected a design office, which he operated in La Courneuve on the Seine, with the French shipbuilding industry. There he developed super-charged four-stroke engines for commercial and naval ships, as well as for locomotives, until 1957.
IT Shake-up in 2009
MAN acquired S.E.M.T. in 2006 and renamed the company MAN Diesel & Turbo France SAS in 2010. It belongs to MAN Diesel & Turbo SE, whose almost 15,000 employees contributed approximately 3.3 billion euros in sales to the 14.3 billion euros in total sales of the MAN Group last year. The illustrious brand name Pielstick continues to be maintained, under which other manufacturers across the world are operating to produce diesel engines under license. Approximately 15,000 engines with a total power output of 45 gigawatts are installed. The power output of each individual engine ranges from 500 to 26,500 kW. They are used not only in ships, but also in power plants and emergency generators.
At the plant in Saint-Nazaire, MAN installs and tests large four-stroke diesel engines and dual-fuel engines that can be operated with liquid and gaseous fuels. Spare parts like connecting rods, cylinder heads, and crank cases are also produced there. Raphaël Cuartero is the manager of Industrial Engineering and Maintenance. “We started the SAP introduction project in spring and then found out that our tool management program was no longer going to be developed,” he recalls in 2009. This led to the migration to TDM, the software from the IT service provider with the same name from Tübingen.
St. Nazaire is the Forerunner in Tool Data Management
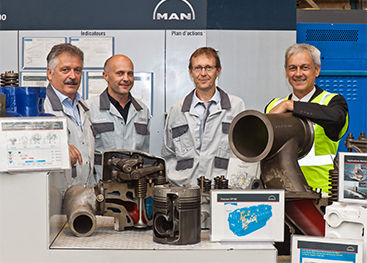
This was a mammoth task for Cuartero and his team, but they did an excellent job of mastering it. Since then, the plant in Saint-Nazaire is considered the forerunner among MAN Diesel & Turbo facilities in terms of TDM. Recalling the critical meeting with his colleagues from the Augsburg plant, Cuartero says, “They asked for comparisons with other tool management software – and in the end, TDM was also implemented in Augsburg.”
In France, they went all in at an early stage and invested in almost all of the integrated Tool Data Management system modules. “In addition to the Base Module, we use the Data and Graphic Generator for turning and rotating tools, the TDM 2D Graphic Editor and the TDM Tool Contour Generator. We also use the TDM Tool Crib and TDM Purchase Requisition Module and TDMcontrol,” Raphaël Cuartero adds. Eight of the over 600 employees in Saint-Nazaire work directly with TDM. “We trained the MAN employees right here on site,” says René Taillade, TDM sales partner in France
Fully Automated Ordering Systems Save Time
The numerous interfaces that the pioneer of digital tool management offers today are an important feature for MAN. They are the specialty of IT manager François Valentin, who says, “Connecting TDM to our new ERP system from SAP could not have gone more smoothly.” This allows the ordering system, just to give an example, to run in a fully automated manner. If the tool storage system of the French manufacturer’s Electroclass SAS signals that the stock level has fallen below the minimum, purchase requisition is triggered. “Earlier we had to do that manually, which was a full-time job,” adds Valentin.
MAN France uses presetting devices from Kelch for installing and presetting tools. “Our easyKELCH interface provides the necessary data,” René Taillade explains. Another interface to the EDGECAM CAM system provides additional CAD functionality for automated conversions and manual editing of 3D tool graphics.
CAD Support is Extremely Important
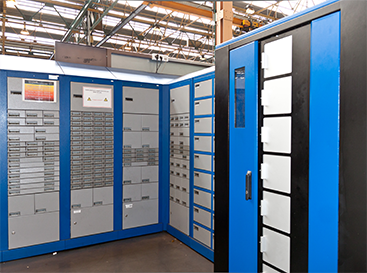
“We have to rework the tool manufacturer’s CAD models frequently and the Graphic Generator’s modules are particularly helpful in doing that,” explains Olivier Truchot, TDM Key User and specialist in metal cutting tools at MAN. “Even if the number is increasing; as of now, 3D data is available for only approximately 30 percent of the tools.” MAN France purchases its tools from, among others, Walter, Sandvik Coromant, Seco, Kennametal, and Gühring. In addition, there are some manufacturers of special tools that account for approximately a quarter of all tools.
Raphaël Cuartero explained using examples to illustrate the quantities involved, “We need approximately 130 tool assemblies that are made up of about 600 items to manufacture a cylinder head or a connecting rod.” Altogether, the plant has approximately 20,000 tools. 3D data from all tools are needed for new products, “because we always simulate them before the manufacturing process using VERICUT, which receives the 3D data via the corresponding TDM interface.”
Networking MAN Plants Using TDM
It is for this reason that many 3D models are created by MAN in Saint-Nazaire, which has generated a great deal of interest in Augsburg. “We would like to avoid the duplication of effort and make the 3D models available in a common database,” says Cuartero. The TDM data is currently still on a server in Saint-Nazaire, explains IT manager François Valentin. But the networking has long since begun, with the goal of improving the flow of information between the plants. The goal is to harmonize the IT landscape at MAN. Wasted effort such as creating multiple 3D models of the same tool should be eliminated in the future.
As a man of numbers, François Valentin does not see the networking as a purely technical challenge. He cites the “end of the silo mentality at the Saint-Nazaire and Augsburg plants” as a central success factor of the TDM project. The employees became substantially closer to one another as a result of the TDM introduction. Through the continuous exchange of best practices, close collaboration is an everyday occurrence now. In this way, TDM even made a contribution to international understanding.
MAN Diesel & Turbo - provider of large diesel engines and turbo engines
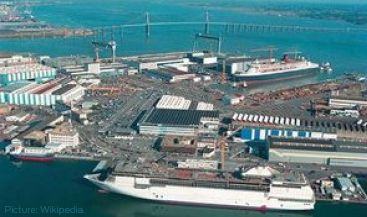
MAN Diesel & Turbo SE (Societas Europaea) based in Augsburg, Germany is a provider of large diesel engines and turbo engines for maritime and stationary applications. The company has approximately 14,400 employees in more than 100 international locations, particularly in Germany, Denmark, France, Switzerland, the Czech Republic, India and in China.