Avec le recul, les responsables du projet de Test-Fuchs s'étonnent eux-mêmes du courage dont ils ont fait preuve. Lorsqu'il a été décidé en 2012 de construire un nouvel atelier de production au siège de l'entreprise à Groß-Siegharts en Autriche, tout a été passé au peigne fin. « Si nous le faisons, alors faisons-le correctement », telle était la devise qui a contribué au lancement de nombreux chantiers en plus de la construction de ce nouvel atelier. La gestion des outils a également fait l'objet d'un contrôle scrupuleux.
« À l'époque, chaque opérateur était responsable de son outil de coupe et exécutait lui-même les travaux de préparation et le préréglage », se souvient Robert Schlosser, directeur de la fabrication mécanique chez Test-Fuchs. « Où est l'outil ? », était la phrase la plus souvent prononcée. La recherche d'outils, la préparation et le préréglage étaient responsables de temps d'arrêt machines extrêmement longs. Une gestion des outils orientée vers l'avenir et une nouvelle organisation s'imposaient. R. Schlosser explique : « Nous voulons savoir à tout moment où et quels sont les outils en circulation. De plus, les outils doivent être prêts et disponibles quand on en a besoin sur la machine. »
Des listes de retrait d'outils à l'Industrie 4.0
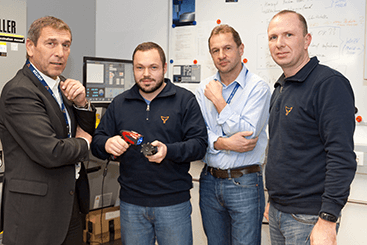
Jusqu'en 2012, les collaborateurs répertoriaient seulement les outils dans le système ERP et leur attribuaient un numéro d'ERP pour conserver un semblant de vue d'ensemble. Les outils étaient stockés de manière centralisée dans des armoires. Mario Samm, un collaborateur qui, outre son poste principal d'opérateur de tour CNC était déjà à l'époque aussi responsable de la gestion d'outils, se souvient : « Nous ne savions jamais où se trouvaient nos outils et surtout dans quel état ils étaient car le retrait des outils était seulement documenté par le biais d'une liste de retrait des outils et n'était noté qu'ultérieurement dans le système ERP. »
Il est rapidement apparu que seule une gestion d'outils extrêmement professionnelle pourrait apporter une amélioration réelle. Après avoir obtenu l'aval du chef de l'entreprise Volker Fuchs, il a fallu se pencher sur la sélection. Nous avons procédé à des recherches, des comparaisons et avons visité des entreprises de référence. « Nous avons finalement opté pour le logiciel de TDM parce que c'est justement là que nous avions observé les meilleures compétences en termes de gestion d'outils ainsi qu'un développement évolutif. »
Dino Velagic, collègue de Mario Samm également chargé de la gestion d'outils, ajoute : « Seul TDM Systems était en mesure de nous proposer l'étendue des fonctions, telle que nous nous la représentions. » L'appui fourni par le leader mondial dans le cadre des préparatifs nous convenait également, et c'est ainsi que mi-2012 la décision en faveur de TDM est tombée. Le logiciel a été acheté en août et l'équipe du projet a pu commencer à travailler dès le mois de septembre.
Ensemble sur la voie du succès
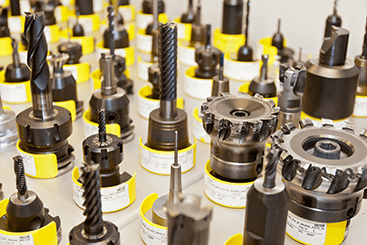
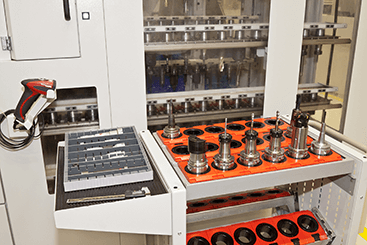
Ça n'a pas été simple pour les deux parties. Ainsi, chez Test-Fuchs, on s'est d'abord montré très respectueux face à cette puissante solution logicielle. Mais, au vu de l'importante fabrication interne qui implique environ 4 000 composants d'outils, c'était la « seule solution appropriée ». Hans-Peter Sindler, consultant TDM, admet qu'avec « l'association de données d'outils dans un système, la mise en réseau avec la programmation CFAO, le dispositif de préréglage, l'entrepôt et l'automatisation ainsi que deux machines et un système d'élevage, Test-Fuchs avait prévu un projet de gestion du cycle de vie des outils à niveau d'intégration élevé qui imposait également certaines exigences à TDM Systems. » Mais tout a fonctionné pour le mieux avec TDM. Hans-Peter Sindler attribue cela au fait que l'on a « élaboré une feuille de route ensemble et que le département d'ingénierie et l'équipe de gestion du projet ont accompagné le projet dans son intégralité. »
Selon Robert Schlosser, le fait que les professionnels de TDM Systems ont d'abord analysé exactement la situation et les objectifs constitue également l'un des plus importants facteurs de réussite. « L'on accompagne le processus de manière intensive depuis le début jusqu'à ce que l'on parle réellement la même langue et que l'on soit ainsi d'accord sur le vocabulaire. » Selon Dino Velagic, le principal obstacle dans le déroulement du projet réside dans la question des interfaces. Elle est de nature fondamentale et dépasse largement le cadre de la gestion de données d'outils. « C'est l'adaptation des interfaces qui demande le plus du temps ; bien que chaque constructeur de machines l'affirme aujourd'hui, la réalité est tout autre. » Son conseil est le suivant : il faut, au préalable, définir de manière exacte les interfaces pour chaque type de projet de mise en réseau. Test-Fuchs en a tiré les leçons et exige des interfaces ouvertes pour les machines-outils, et en fait même un critère essentiel dans les nouveaux investissements. Au moins, tout a fini par fonctionné avec TDM. Hans-Peter Sindler déclare : « aujourd'hui, l'installation chez Test-Fuchs Industrie 4.0 fait partie du quotidien. »
Utilisation étendue de TDM
Outre le TDM Module de Base comme condition, l'équipe responsable du projet chez Test-Fuchs a opté pour le module de préréglage. À cet effet, l'interface TDM adaptée était essentielle pour le dispositif de préréglage déjà présent. L'interface des systèmes de stockage constituait aussi le critère décisif lors du choix du TDM Module de Stock. Car c'est justement par ce biais que TDM communique avec la navette à outil de Kardex. TDM propose d'autres interfaces importantes pour la cellule d'automatisation de Promot Automation, le système ERP de Famac et les deux systèmes de CFAO de TopSolid et Alphacam. TDM Systems propose également des solutions pour remplir la base de données : Le TDM Générateur de Données et Graphiques avec ses 68 000 outils de fabricant pouvant être appelés par simple clic et complété par divers modules graphiques TDM, sert à la composition rapide de graphiques en 2D et 3D de composants comme d'outils complets.
Grâce à TDMshopcontrol, il est également possible d'intégrer des machines autonomes dans le circuit de l'outil. Quand il faut aller vite, TDMcontrol apporte son aide. Le format du tableau permet de procéder à différentes modifications dans le système. La formation proposée par Test-Fuchs aux collaborateurs était aussi variée que les modules : Les formations relatives à l'utilisateur système, au module de stock, aux données et au générateur de graphiques, ainsi qu'au contrôle du magasin facilitent les premiers pas dans l'univers de la gestion des données d'outils.
Un savoir-faire accessible à tous
Si un module exige un nouvel outil, Test-Fuchs utilise d'abord le processus d'acquisition classique et lance un appel d'offres. Une fois l'outil défini, Mario Samm ou Dino Velagic le créent dans le système ERP. Les géométries associées spécifiques à l'outil, les graphiques en 2D/3D et d'autres données, ainsi que l'emplacement de stockage et les données concernant la durée de vie fournies par le constructeur, sont saisis dans TDM. Ensuite, ils créent avec l'enregistrement de la machine actuelle un outil virtuel complet en 3D qui sert de modèle aux programmateurs CN.
Pour chaque programme CN, il y a une liste d'outils. Celle-ci est exportée du système de CFAO vers TDM et constitue, via TDMshopcontrol, la base du montage et du préréglage pour le processus de préparation des outils. Si nécessaire, les composants réels sont assemblés en outils complets de manière centralisée dans l'entrepôt, et non plus sur la machine comme autrefois, et ainsi mis à disposition à temps avant le début de l'usinage sur la machine concernée. Les valeurs de coupe du catalogue peuvent être complétées par les opérateurs et ainsi optimisées en permanence. Les programmateurs CN peuvent également ajuster et créer des valeurs de coupe. Par conséquent, d'autres jeux de données sont créés au fur et à mesure pour chaque outil. Robert Schlosser explique : « Même les collaborateurs ayant peu d'expérience avec certains outils repèrent immédiatement les valeurs de coupes logiques. » De ce fait, TDM devient également un système de connaissance pour l'usinage par enlèvement de copeaux dans l'entreprise.
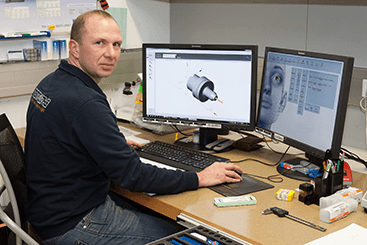
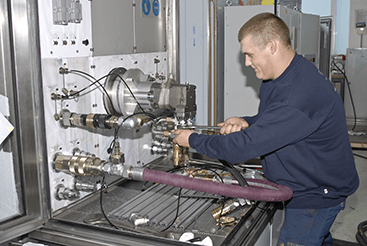
Un acteur mondial d'Autriche
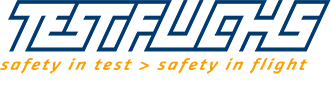
L'entreprise a même fait de sa profession un nom : « Test »-Fuchs, créée par l'ingénieur Fritz Fuchs en 1946. Depuis les années 1950, l'entreprise conçoit et fabrique des appareils de test, au départ pour le domaine automobile, puis pour l'aéronautique. La percée dans cette branche exigeante a eu lieu dans le courant des années 1960 dans le cadre d'une collaboration avec l'armée de l'air allemande.
Des filiales ont été ouvertes aux points de jonction mondiaux de l'aviation ; d'autres secteurs de production, tels que la fabrication et la maintenance de composants pour hélicoptères, petits avions et régulateurs et ventilateurs pour le domaine aérospatial s'y sont ajoutés. Depuis plus de dix ans, l'aviation civile représente l'axe essentiel des activités de l'entreprise. Aujourd'hui, Test-Fuchs est l'un des principaux fabricants au monde de systèmes d'essai pour la production d'avions et la maintenance d'avions. À cet effet, l'entreprise exploite des filiales en Allemagne, en Grande-Bretagne, en Italie, en France, en Espagne, à Singapour et depuis peu aux États-Unis.
L'éventail des équipements de test s'étend des appareils et installations standardisés jusqu'aux solutions de pointe telles que les pièces uniques spécifiques aux clients, en passant par les systèmes de test modulaires. Le portefeuille de produits englobe les appareils de test pour les composants hydrauliques, électriques/électroniques, pneumatiques ou fonctionnant au carburant. La production de ces appareils par Test-Fuchs implique une fabrication interne importante de 65 à 70 %, opérée exclusivement à Groß-Siegharts.
Aujourd'hui, l'entreprise est dirigée par la troisième génération représentée par le directeur général de 41 ans Volker Fuchs, qui est appuyé par le directeur financier Armin Havlik et le directeur de l'exploitation Dr. Markus Nagl. L'entreprise emploie 420 collaborateurs, dont 380 à Groß-Siegharts, et a réalisé un chiffre d'affaires de 50 millions d'euros pour l'exercice 2015/2016. Avec un quote-part d'exportation de 95 %, la PME qu'est Test-Fuchs s'élève au rang des acteurs mondiaux.