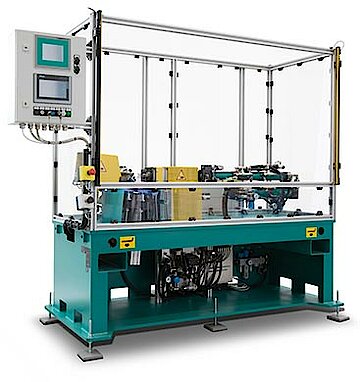
La pression concurrentielle mondiale devient également du plus en plus dure pour TOX PRESSOTECHNIK. C’est la raison pour laquelle l’entreprise, qui produit à l’international, souhaite produire de manière encore plus efficace qu’auparavant. La solution TDM a été introduite dès 2008 sur le site de Weingarten, puis a été étendue au fil du temps, de sorte à obtenir une solution complètement intégrée. Des améliorations innovantes des processus et des économies considérables en sont le résultat. Mais qu’est-ce qui a changé, au juste, avec l’application TDM ?
Avant l’introduction du logiciel TDM, TOX PRESSOTECHNIK gérait ses outils à l’aide de listes. Avec 16 machines de fraisage fonctionnant en permanence et devant être rééquipées huit à onze fois par équipe, c’était « une véritable catastrophe ». « Personne ne savait exactement où étaient utilisés ou se trouvaient les différents outils , explique Markus Kuhn, spécialiste en programmation FAO & gestion d’outils. Un problème qui mettait en péril la sécurité de production et la qualité et faisait grimper les coûts d’outils et de stockage.
Moins d’outils et des coûts en baisse
L’introduction de TDM a entraîné un changement radical de la situation. Il a ainsi été possible de réduire sensiblement la diversité et les stocks d’outils malgré la croissance du chiffre d’affaires. Actuellement, 4985 différents composants d’outils sont en stock, soit 20 pour cent de moins qu’il y a cinq ans. Pour consolider les stocks, TOX PRESSOTECHNIK a entre autres défini dans TDM des outils standards pour chaque machine. Il n’est en outre plus nécessaire de stocker les outils supplémentaires requis en deux ou trois exemplaires. « Avec TDM, nous pouvons planifier la production de manière à ce qu’un seul et même outil spécial soit utilisé pour différentes commandes. » Plus qu’un simple effet secondaire : grâce à la réduction de la diversité d’outils, TOX concentre également davantage ses besoins.
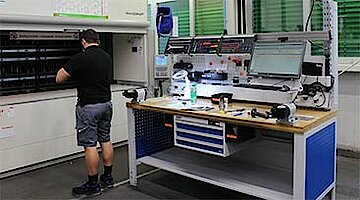
Transparence grâce à la connexion d’armoires de stockage
Le système de distribution permet une réduction supplémentaire des coûts. Les armoires de stockage sont pilotées et gérées à l’aide de TDMstoreasy. Outre les outils, les armoires contiennent également des consommables. Les articles prélevés sont directement attribués à une machine. La conséquence : « une consommation bien plus faible aujourd’hui ». De plus, il est possible de se réapprovisionner de manière plus ciblée. Et grâce à la définition de limites de réapprovisionnement, « nous maîtrisons parfaitement la situation, même avec des milliers d’articles. »
À la réduction considérable des coûts d’env. 25% au niveau de l’approvisionnement et du stockage vient s’ajouter des une réduction sensible des temps de préparation, d’après le mécanicien spécialisé en usinage.
Temps de préparation réduits au strict minimum
Grâce à la définition d’outils standards, « l’outil requis se trouve, idéalement, déjà sur la machine et nous n’avons plus besoin de la rééquiper », explique Kuhn. Et même si de nouveaux outils devaient être nécessaires, leur montage est aujourd’hui « un jeu d’enfant ».
La grande différence par rapport à avant, c’est que toutes les données d’un nouvel outil sont déjà enregistrées dans la machine et disponibles lorsqu’il est utilisé pour la première fois. « L’outil a déjà parcouru toute la chaîne et est prêt à l’emploi. Ce n’était pas le cas autrefois. Cela nous a permis de réduire nos temps de préparation au strict minimum, » déclare Kuhn.
Mesure d’outil intégrée
La capacité d’intégration et l’ouverture du système TDM à d’autres systèmes permettent une optimisation notable des processus dans l’ensemble de la production. « Aucun autre système sur le marché n’est actuellement aussi complet en ce qui concerne les interfaces », déclare Kuhn. La connexion des appareils de préréglage est un excellent exemple de la capacité d’intégration de TDM.
La laborieuse saisie manuelle des données de consigne des outils devient ainsi superflue. Celles-ci sont fournies aux systèmes de préréglage par TDM. Les données réelles mesurées sont ensuite transmises par le système de préréglage, via TDM, à la machine d’usinage. La saisie manuelle des données, chronophage et source potentielle d’erreurs, appartient ici également au passé.
Source d’erreurs éliminée grâce à l’interface vers le système FAO
Pour Kuhn, l’interface entre TDM et Creo, le système FAO utilisé par TOX PRESSOTECHNIK, est d’une importance toute particulière. Si aucun outil complet convenant à l’opération d’usinage n’est disponible sur la machine, les programmateurs CN recherchent un outil approprié dans TDM ou ont recours à de nouveaux outils.
À côté des méthodes de filtrage en fonction des paramètres ou du matériau de coupe, ils ont accès à des graphiques 2D et 3D des outils. Toutes les données d’outils complets nécessaires à la programmation CN, y compris les paramètres de coupe, sont alors transférés par simple pression d’un bouton, via une interface, de TDM au système FAO Creo. Le transfert des données est non seulement rapide et confortable, mais aussi exempt d’erreurs. Et les données d’outils étant désormais gérées et mises à jour de manière centralisée dans TDM, TOX PRESSOTECHNIK réalise un gain de temps important au niveau de la maintenance des données tout en assurant que « chacun travaille avec des données actuelles et valides ».

Données d’outils pour la simulation
Une fois la programmation CN terminée, TOX PRESSOTECHNIK vérifie par des simulations numériques effectuées avec le logiciel de simulation CNC de HEXAGON que la fabrication des pièces se déroule sans collision sur la machine avec les outils sélectionnés.
Une démarche qui porte ses fruits : depuis 2013, TOX PRESSOTECHNIK n’enregistre plus de collisions dues à un assemblage incorrect des outils. Selon Kuhn, la qualité des données d’outils est cependant toujours d’une importance primordiale et « doit tout simplement être garantie ». Les fabricants d’outils qui ne lui livrent pas de données compatibles FAO ne sont par conséquent pas acceptés comme fournisseurs.
Augmentation sensible de la durée de vie des outils
Si la simulation s’est déroulée sans incidents, les listes d’outils sont transférées du système FAO à TDM. Elles servent ensuite de base pour la planification des outils pour les machines dans TDMshopcontrol.
Chez TOX PRESSOTECHNIK, les durées de vie des outils ont ainsi pu être allongées de 30 pour cent et le taux de rebut être réduit de manière significative au cours des dernières années. Des résultats « qui n’auraient pas été possibles » sans TDM, d’après Kuhn. Pour lui, une chose est claire : « TDM est le système le plus important pour nous, dans le domaine de la fabrication mécanique – après SAP et Felios ». TOX PRESSOTECHNIK souhaite par conséquent également l’utiliser à l’échelle internationale à l’avenir.
Situation avant l’introduction de TDM
- Aucune vue d’ensemble des outils, des emplacements de stockage et des stocks disponibles
- Sécurité de production et qualité non garanties
- Coûts d’outils et de stockage élevés
Innovation en matière de processus
- Une base de données d’outils centrale met des données actuelles et valides à la disposition de tous les services
- La distribution automatisée d’outils et de consommables réduit la consommation et permet un réapprovisionnement ciblé
- L’intégration dans les processus et procédures d’autres systèmes permet d’obtenir des processus de haute qualité et de réduire les erreurs
- Haute qualité des programmes CN et des analyses de simulations - plus aucune collision depuis 2013
- Des machines rapidement prêtes à fonctionner grâce à la définition d’outils standards pour chaque machine
Interfaces
- avec Zoller, Fastems, le système de stockage Hänel, le système de FAO Creo et le système ERP SAP
Processeurs de offset d'outils
- Heidenhain et Siemens