L’entreprise familiale BRUDERER, considérée à l’échelle internationale comme une pionnière de la technologie de pointe, emploie environ 460 collaborateurs dans le monde, dont 370 à Frasnacht, en Suisse. C’est à Frasnacht que la PME développe et produit depuis plus de 75 ans les machines automatiques de découpe destinées au monde entier. Et comme toutes les entreprises des pays industrialisés développés, BRUDERER est confrontée au défi de maintenir ses coûts de fabrication à un niveau compétitif pour faire face aux coûts salariaux élevés.
Un précurseur visionnaire
Afin de garantir la transparence de la gestion d’outils et d’épargner aux programmeurs FAO des recherches chronophages, BRUDERER a décidé, il y a exactement 30 ans, d’introduire une gestion numérique des outils de TDM Systems. Michael Fankhauser, responsable de la gestion du système et, entre autres, de l’introduction de TDM chez BRUDERER, est employé dans l’entreprise depuis 1983 et s’en souvient encore parfaitement. À l’époque, c’étaient les contremaîtres qui commandaient les outils requis, ce qui a conduit, à un moment donné, à une prolifération incontrôlée et une situation confuse. En raison de l’absence de transparence concernant les outils existants et leurs données, la programmation CN prenait beaucoup de temps. C’est ce qui a poussé BRUDERER a devenir, en 1991, l’un des premiers clients en Suisse à introduire la gestion numérique des outils de TDM Systems.
La numérisation permet de réduire les coûts d’approvisionnement de 30%
Pendant cette période, BRUDERER a consacré deux années-hommes de travail à la saisie d’environ 5000 composants. Selon Fankhauser, cette tâche s’est rapidement rentabilisée. Très rapidement, la transparence obtenue a permis de réduire d’environ 30% les coûts d’acquisition des moyens de production. Grâce aux graphiques disponibles, la fréquence des erreurs d’assemblage lors du montage des outils a sensiblement baissé. Mais ce sont surtout les programmeurs FAO qui ont bénéficié de ce progrès : la création des programmes prenait désormais également moins de temps.
TDM - le logiciel le plus important au sein du processus de production, derrière le PGI
Pendant plus de 20 ans, BRUDERER a utilisé la solution TDM pour la gestion de ses outils. Mais avec l’extension de la solution de gestion d’outils, l’entreprise suisse a souhaité, il y a un peu plus de 10 ans, exploiter encore davantage le potentiel des données d’outils, ce qu’elle a atteint en 2011 grâce à la mise à niveau à TDM V4 qui a « apporté une toute nouvelle dynamique » selon Fankhauser. Petit à petit, BRUDERER a introduit de nouveaux modules et de nouvelles interfaces. Une décision qui fait aujourd’hui de TDM le second logiciel le plus important pour la fabrication de l’entreprise suisse, après le système PGI. « Sans TDM, aucun outil ne peut être utilisé sur les machines intégrées et aucune commande ne peut être traitée », explique Fankhauser.
Projet d’avenir : l’intégration des machines
« Nous voulons que les processus soient aussi sûrs que possible. Cela signifie également qu'il faut éviter autant que possible les transmissions manuelles », explique Fankhauser. L’objectif de l’équipe BRUDERER très investie était un échange continu de données entre TDM et les machines. Même si cela semble très simple, cela n’est réalisable qu’avec une planification intelligente et un investissement correspondant dans le projet. En effet, il n’existe actuellement aucune solution globale. De plus, seuls quelques fabricants de machines ou développeurs de commandes de machines permettent le transfert bidirectionnel de données via une interface interne. Le développement d’une interface avec la commande de la machine pour transmettre des données d’outils complètes est donc un projet ambitieux. Comme le précise Fankhauser, cela dépend de multiples facteurs comme le type de machine ou encore le logiciel de commande utilisé.
Réaliser le potentiel d’optimisation
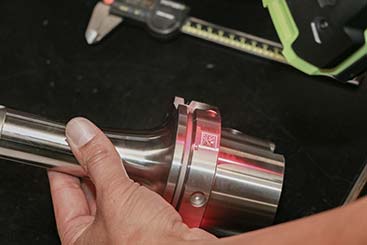
Étant donné que l’équipe BRUDERER s’attendait à ce que l’intégration des machines dégage un potentiel d’optimisation considérable, elle a décidé de se lancer dans le projet. Et, comme en 1991, l’entreprise fait partie des précurseurs, et pas seulement dans son secteur. Il a fallu un peu plus d’un an aux développeurs pour pouvoir transférer les différentes données d’outils de TDM vers les commandes de machines que BRUDERER utilise. Pour cela, TDM Systems a fait appel à un partenaire de développement, l’entreprise ECI. La box ECI est une sorte de middleware qui prend en charge l’échange de données entre TDM et la commande de la machine.
Communication bidirectionnelle des données avec la machine
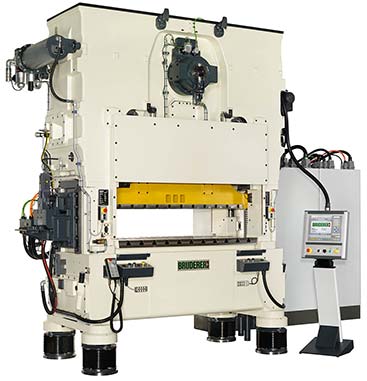
Comme Fankhauser l’explique, l’intégration des machines mise en œuvre est en fait une extension du module TDM Shopfloor Manager. Celle-ci permet, en plus de la planification des besoins en outils et de la mise à disposition des outils nécessaires, de prendre en compte les stocks réels de machines et l’état des outils. Par exemple : l’interface ECI transmet les durées de vie réelles des outils utilisés à la base de données TDM. Il s’agit ici d’un point important en matière de sécurité du processus, car on ne travaillait auparavant qu’avec des valeurs empiriques et des suppositions. Désormais, celles-ci sont toujours vérifiées à l’aide de données réelles provenant de la machine, et l’on constate depuis un allongement de la durée d’utilisation des outils.
Moins de temps de préparation grâce à la surveillance de la durée de vie
Autre avantage : un feu tricolore avertit l’opérateur lorsque la durée de vie des outils atteint un seuil critique. Il est ainsi possible de prévoir plus facilement le remplacement de l’outil et de s’assurer qu’il sera disponible lorsque la durée d’utilisation arrivera à échéance. En outre, le temps nécessaire à la préparation de la machine a également diminué. L’inventaire des outils au niveau de la machine étant transparent, seuls les outils qui ne sont pas couverts par celui-ci sont encore assemblés. Tous ces éléments permettent à BRUDERER d’exploiter encore mieux les capacités de ses machines.
Moins d’erreurs et d’arrêts de machine
Toutes les données d’outils nécessaires à la fabrication sont directement transmises par TDM à la machine, et ce sans aucune saisie manuelle de données. Pour procéder au transfert des données, les opérateurs de la machine n’ont qu’à scanner le code Datamatrix sur l’outil et à insérer l’outil dans l’emplacement de magasin correspondant. Grâce à ce processus, « plus aucune erreur de transmission ne peut se produire », affirme Fankhauser. BRUDERER est encore en pleine phase de test étendue. L’entreprise est actuellement en train de saisir et d’analyser les données. Toutefois, les premières évaluations montrent que l’interface assure une sécurité accrue des processus. « Depuis que les données sont automatiquement transmises aux machines de production, aucune erreur d’usinage ou de collision due à des données d’outils erronées ne s’est produite », déclare Müller.
Premier jalon du développement numérique
Chez BRUDERER, les machines ne s’arrêtent plus pour la saisie des données, et cela est d’une grande importance. En effet, avant l’introduction de l’interface, certaines commandes de machines ne permettaient pas de continuer la fabrication pendant le transfert manuel des données. Avec plusieurs processus d’équipement par jour, les temps d’arrêt des machines s’accumulaient de manière significative. Pour Fankhauser, une chose est claire : « L’intégration de nos machines de production dans la solution TDM est définitivement un point positif. » Et pas seulement parce que cette intégration permet une production plus efficace. Elle est aussi le premier jalon du développement numérique de l’organisation de la fabrication chez BRUDERER. Par ailleurs, elle épargne également aux opérateurs des machines les travaux de routine à effectuer manuellement et permet ainsi, comme l’affirme Müller, de « rendre les postes de travail plus attrayants chez nous dans la gestion d’atelier ».
Objectifs de BRUDERER
- Des processus parfaitement sûrs avec la gestion d’atelier
- Éviter la saisie manuelle des données sur la machine
- Connexion continue des données à la machine
- Réalisation d’un potentiel d’optimisation tout autour de la machine
Innovation des processus grâce à la connexion à la machine
- Transfert automatique des données d’outil à la commande de la machine, déclenché par le code Datamatrix sur l’outil
- Connexion bidirectionnelle des données à la machine
- Préparation des outils complète, transparente et efficace prenant en compte
- l’état réel des outils et du parc de machines
- les besoins en outils par ordre CN ainsi que
- les durées de vie surveillées en continu via le système de signaux visuels
- Vérification constante des données de planification en assurant le retour des données depuis la machine