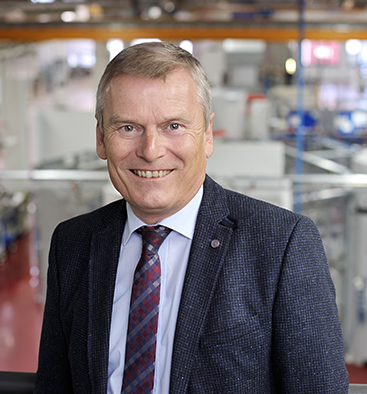
Mr. Schneck, TDM Systems is announcing a new development phase in its market segment with the term "Tool Lifecycle Management". What's behind all this?
Software for Tool Data Management has emerged to better organize tool variety in production. In the recent past, information technology has developed new possibilities for simulating tool use, especially in the area of 3D. In Tool Lifecycle Management, this entire process is the focal point – from the definition of the tools to their use in planning to seamless transfer and use on the shopfloor. What's especially new about this is that the information from each individual process step flows back, continually improving the data.
The information loop between planning and manufacturing is closed?
Exactly. An information deficit between planning and the production process is still the standard today. However, the production engineer has to depend on that he will receive information about how the real situation on the shopfloor is. An integrated system is necessary for this that includes the manufacturing process and supplies information about tool life at the machine, history of the tool, when it needs to be resharpened or replaced right up to returning it to the tool crib or scrapping it. However, even standardization on the shopfloor using predefined tool lists can be implemented with an integrated solution.

More knowledge about the tools: What does the company get out of it?
The real-time operation of the machine can be significantly reduced again. There are primarily two drivers for the optimization of tool data management: Cost efficiency on the shopfloor and the required documentation on the origin of products, which includes the operating equipment. Both strategic goals are closely linked to Tool Lifecycle Management.
Will Tool Lifecycle Management be an important part for Industry 4.0?
The smart factory, that is, the vision of how production becomes completely virtualized, is important for our portfolio in the machining domain. To this end, it is important that the planning be as precise as possible and that the machining of metal be simulated in a virtual machine room with a virtual tool. We support the concept of Industry 4.0 with our lifecycle approach by providing a complete overview of the machining process using logic and 3D-graphics.
What role does the Internet of Things play?
The Internet is growing in significance in the collaboration between companies. For optimum control of global processes, it will be necessary to build a bridge between one's own network and the networks of suppliers, partners and customers – this carrier system will be the Internet. This will make it easier to collect information about the setup as well as the selection of the tools. As a result, companies that manufacture internationally are able to implement internal production standards transparently. TDM Systems develops cloud services so that tool data are available via the Internet at the local level at all times.
On the shopfloor, one traditionally thinks in proprietary systems. How important are greater openness, standards and communication in the industry?
ur highest priority is the development of interfaces: to link CAM systems, presetting and crib systems, and machine controls, but also at the planning and execution level, to PPS, ERP and MES systems. TDM Systems already offers multiple connections to various systems that support the manufacturing process. It will be a major advantage when manufacturers comply with international standards (laid down in ISO 13399) when describing and classifying tools. Know-how protection from openness has been the credo in our industry up to now. Indeed, whoever wants transparency and comprehensive integration will have to be more open. This change would have to come from top management.
The great benefit of Industry 4.0 is that manufacturing shifts back into the focus of company management's interest. Digitization and globalization sustainably change the production. Thinking must shift in the direction of openness and networking.
There are many providers in Tool Data Management. What advantage does TDM Systems have over competitors?
We brought our software onto the market as pioneers 25 years ago. Having both the know-how about the manufacturing process and the graphical design of 3D tool data, we became an indispensable system partner for many manufacturers. Many of our competitors have their strength in one segment of the lifecycle. What makes us different is our holistic approach and looking ahead to the future. With modern system solutions, we are adapting to the global, digital and mobile lifecycle management of the creation, selection and use of tools, thus making our contribution for a modern, future-oriented shopfloor.