Systemless: Searching for tools the number one reason for downtimes
Digitalization at WOMA began at the shopfloor's bottleneck: Tool dispensing. "It wasn't unusual to spend a lot of time searching for tools," explains Florian Ruff. "Colleagues were hoarding their tools or storing them with no kind of system or structure. When a particular tool was needed, the machines would be shut down for hours while everyone was looking for a particular tool in a panic." Florian Ruff trained as a machine operator at WOMA and was very familiar with the day-to-day challenges of tool provision. In 2018, he was put in charge of implementing TDM for tool crib management. It was no mean feat for him, and he considered how to go about it down to the very last detail: Determining crib structures and continuous article descriptions, defining a crib system and cost centers, and dispersing unlisted stock on machines. Structures and processes are one aspect; the other major challenge is tool data management. "The database is the basis for everything. This is where we can document what the tools have been used for and to what use they are suited," says Ruff. That was only possible in an unsatisfactory way with the previous system. Clear documentation of tool use was one of the main objectives of the project, alongside transparent tool cribs.
Great efficiency: Tool assembly and provision has become much quicker
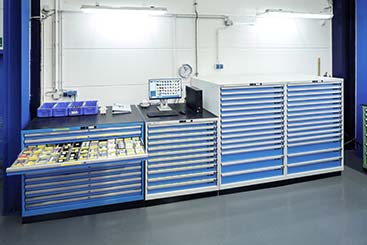
In 2019, the pump manufacturer moved into a new hall and Florian Ruff began the next step in expanding the TDM application. In addition to new LISTA drawer cabinets, investment was also made in a Grob CNC machine, which was loaded with a palette system. Ruff integrated these improvements into his storage concept, developing the details of stock locations and tool preparation processes. Tool dispensing has been running automatically since. Machine operators have been trained and can now access the required tools and consumable items regardless of shift. The next upcoming tools are assembled with a lead time, which is a process that now runs calmly and efficiently. Dispensing at the tool crib now takes just a few minutes. "Hectic searching is a thing of the past for us all. Now we know where each tool is and can spend our time on correct tool assembly," explains Ruff. All the information required here is available via the TDM software. Tool lists have been created as standard for each machine. These not only indicate individual tool items, but also spare parts.
Your own expertise: Feeds & speeds and tool life
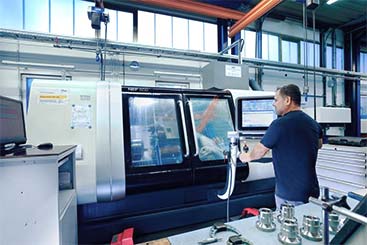
Cutting data is also saved, making selection of the correct tool much quicker and easier. "In TDM, you can simply filter to see which operation in what material takes what amount of time with which tool." This facilitates selection of the best tool for an operation. "Thanks to the tool life and intervention times saved in the tool list, TDM can make a theoretical prediction as to how long the tool will be in use." That's a huge help in tool planning and provision of tools required. "We use this to organize provision at a high level, which ultimately leads to greatly reduced machine downtimes." "All the data you need for tool assembly and setup is in TDM. Swapping out and assembly can be done many times more quickly than before. And what really creates added value is information about spare parts. If a tool has to be replaced during the night shift, machine operators now know immediately which tools to find and where to find them." In this way, Florian Ruff has created a seamless tool circulation process that is traceable at all times.
Significant added value: A central tool database provides yet more advantages
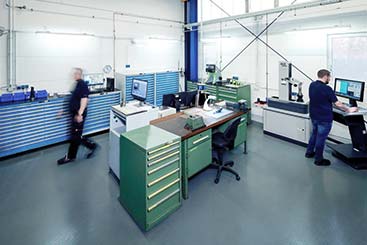
It wasn't only downtimes and setup times that WOMA was able to reduce to a minimum. "We can use the utilization times recorded for the tools to compare them better, as well as use them better, since the information is now just there. We can see which processes run better with which tools, and can therefore schedule the tools," explains Florian Ruff. Florian Ruff was also able to make great progress with tool stock management. Using what is known as "Hit list management" in the Tool Crib Module, he regularly checks usage of all stored items. Tools that have not been used for a long time are regularly withdrawn, thereby gradually creating use-oriented tool stock, removing items that are not being used and making room for stock locations for items that are actually needed.
Keeping an eye on costs: Tool stock visible at all times
Florian Ruff is enthusiastic about what he and his colleagues have improved thanks to TDM tool management. "The time of searching for tools is long past," he says proudly. Finally, he is keen to highlight one further advantage: TDM's inventory list. He can create an inventory list at lightning speed using the TDM Tool Crib Module. Since he has saved the item price for each tool in TDM, all the information needed for the inventory is already there. "I also use the inventory list regularly to check the stocks and tooling costs, which have significantly reduced compared to before. You can also see the effect on orders for new tools – before, we ordered 15 new tools per month, but now we only order around three." WOMA now carries out the inventory in two days with one person, rather the two weeks and several people that was needed to count the tools before.
Impressive figures: Permanent reduction in tooling costs by 20%
WOMA's figures are testament to the fact that a tool management system is worthwhile, even for companies with a small number of machines. The parts for high-pressure pumps are manufactured using 600 tool assemblies on ten machines (turning, milling, grinding). There are 28 employees who work in metal cutting with the tools and machines and three who create the NC programs. In the years 2016–2018, before the introduction of TDM, tools with a value of around €250,000 were procured annually. In 2019, the first full year of operation after TDM had been introduced, these costs had decreased to €200,000. What's more, production management also estimates that they will save approximately 20% of tooling costs per year, in any case €30,000–35,000. "This means that the TDM software pays for itself with the savings made in tool procurement in just the first year," says Florian Ruff, satisfied.
Florian Ruff: Self-taught tool management specialist
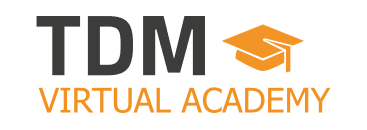
Florian Ruff and his team can certainly be proud of themselves and their achievement. He has focused a lot on TDM software, gaining valuable information from the TDM Virtual Academy. You could also call him a self-taught tool management specialist. "I was glad to have a reliable contact person in the TDM service to answer my questions. The colleagues there provided me with a great deal of support." It was primarily the service's expertise and easy accessibility that formed the foundation of his success. And for anyone considering implementing a tool management system, he has some advice: "Implementing a TDM system is a marathon, not a sprint. But with perseverance and strategy, you can achieve huge improvements."
Prior to implementation of TDM
- No overview of stock locations, available tools and stock
- Significant time spent on searching for the correct tools and time delays in production
- Missing documentation and information on the shopfloor
Process innovation
- Introduction of central TDM database, which optimally manages stock, crib location and tool utilization possibilities
- Automatic tool dispensing in shift operation for smooth production
- Analysis of tool use thanks to saved utilization times, enabling the best possible tools to be determined
- Standard tool lists for each machine offer proactive tool preparation and ensure seamless machine loading
- Optimization of tool stock thanks to determination and sorting of items that have not been used for long periods