First, a little background: Wagstaff is a key player in the aluminum industry, a leader in the design and manufacture of the systems and equipment needed to produce primary aluminum ingot and billet using direct chill (DC) casting methods. Their Spokane facility measures 133,000 sq.ft. and houses R&D, fabrication, machining, assembly, testing and shipping. They have about 30 CNC machines and 20 non-CNC machines.
But they didn't get there overnight. This American success story began in 1946 in a pump-house behind George Wagstaff’s family home. That first year, George, a skilled machinist, used a war-surplus lathe to make sub-contracted parts for another machine shop. During the day, he worked at the lathe and during the night he worked at the Kaiser Trentwood Aluminum plant. Over time his hard work paid off allowing him to purchase a second lathe and expand his machining business. The family business has been expanding ever since. From the 1960s on, under the leadership of George’s son, Bill Wagstaff, the company became the recognized leader in DC aluminum casting technology.
Today, Wagstaff is led by the descendants of George Wagstaff, including his granddaughter, company President Barbara (Wagstaff) Parkes. Wagstaff has subsidiary facilities around the globe and has over 300 customers in 58 countries.
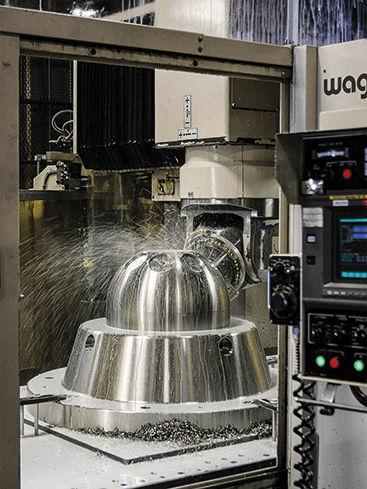
A growing company also faces many challenges, as Jeff Smutny, manufacturing engineering manager at Wagstaff, explains. "At a certain point, about 2004, we realized just how much money we were spending on lost information. Information was stored in process documents for particular product lines and some information resided in our CAM system and also some information resided in Excel spreadsheets. Keeping track of that information and leveraging it on new jobs was difficult. It just wasn't very efficient and everybody seemed to have a little bit different take on how particular tools were used. It was costing us time and money."
Russ Rasmussen, manufacturing engineering technician at Wagstaff, remembers it well. "Everybody had their own way of dealing with the information, and where they kept the information varied. The information wasn't necessarily being shared amongst different users," Rasmussen adds. "For instance, information wasn't always adequately communicated between NC programming and the shop floor. We didn't have a database where the native information resided, so it would get changed or cloned and mutated. People were running on second hand information instead of the source information."
This made it very challenging to perform vital operations like simulating a part program and knowing that you were using the current, correct information.
Needed data

That situation began to change in 2005 when Smutny, as a guest of Walter and Wagstaff’s local Walter distributor, visited the Walter headquarters in Germany. Smutny saw that Walter was using TDM System's Tool Lifecycle Management system in its own shop and he was impressed by its scope and capabilities. "Our people had been considering tool presetters for some time but the data management utilities were weak," recalls Smutny. "After seeing the TDM system in operation, it was clear we needed to get a tool management system before we got a presetter.” Furthermore, he noted that, “Walter was using TDM interfaced with the same CAD system and the same part program verification system that Wagstaff used.”
"Tool Lifecycle Management ensures that tool data is available where it is needed, when it is needed," explains Dan Speidel, director of sales for TDM Systems. "It links CAM systems, presetting and crib systems, as well as CNC machine controls, but it can also extend upstream to the planning and execution level, such as PPS, ERP and MES systems. To extend so widely, a Tool Lifecycle Management system must be open and able to supply numerous import and export interfaces, and to integrate data from various sources, such as manufacturer catalogs or 3D models created in house, into a centralized database."
Speidel adds that the system collects data from production and transfers this data to other systems. Tool Lifecycle Management impacts the entire process from the selection of tools, to their use in production planning, to seamless transfer and use on the shop floor. Information from the individual process steps continuously flows back to a centralized database creating a growing mass of data that's accessible throughout the networked system. It was a system that was sorely needed.
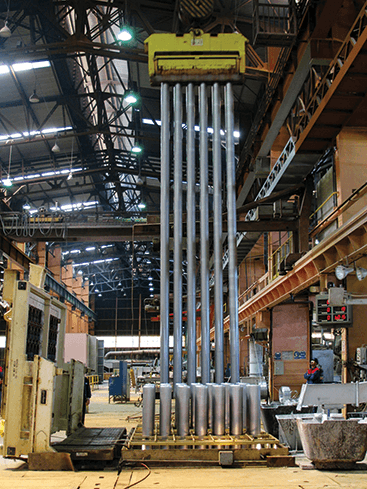
"Wagstaff had the typical standalone silos of information that we see in so many companies," says Speidel. "The old process was to get a job and turn it over to mfg. engineering to design and plan the process, then turn it over to NC programming. Once the NC program was defined, they would walk the program to the tool crib and look for the tooling for the job. They would look in their stash and the machine operator would often need to look through his stash. Of course, everyone has their own preference for tooling." It was not consistent nor was it efficient.
“The shop had numerous tooling racks in a variety of locations,” Rasmussen notes, “but there was no way to digitally search for all of the tools so the employees had to walk around and search. The central tool crib primarily sharpened tools and tried to maintain stock levels.”
"They had tooling data everywhere," Speidel continues, "in Excel spreadsheets, Word tool lists, tool crib index cards, on Note Pad, on people's individual drives, in shop travelers, in tooling books at the machines, or simply in their head. The key point is that there was no central tooling system and this information wasn't digitally traceable or searchable. They also had Vericut from CGTech to verify tool path but the tool information in that system wasn't fully integrated with the CAM system.”
This is not to throw stones at Wagstaff as many companies have found themselves in this position, the difference is that Jeff, Russ and Howard Estes (now retired) were determined to do something about it. The key driver for them was that they realized they needed to become more organized in terms of their tooling information and to capitalize on the wealth of tribal knowledge that had been built over decades of manufacturing highly engineered products.
Tool Lifecycle Management
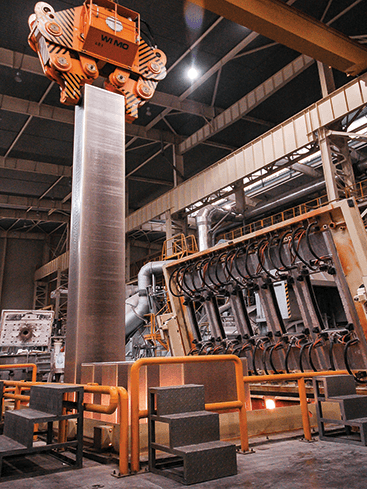
Getting organized began with the actual definition of the tools, the first step in Tool Lifecycle Management. This was no easy task for Wagstaff since, as Rasmussen notes, "We've got approximately 4,000 tool assemblies and many, many more tool components."
Speidel notes that companies often content themselves with the CAM system's generic tool models, but there is a price to pay for that. How many times, he asks, have you seen programmers leave their desk and go down to the shop looking for the right tool, or going to the tool crib to ask, do we have something like this? If your NC programmers can't search the access database for information about the contents of the tool crib, then they've got to get up and look for the tool or tools in question. The result: lost time.
Using the actual tool graphics, not generic tool models, takes the guesswork and uncertainty out of tool creation. When the individual tools and components are identified specifically, efficient and repeatable accuracy can be attained.
Other questions arise during tool selection, such as which tools are best suited for which process steps? Which combinations are most efficient? TDM's Tool Lifecycle Management helps Wagstaff quickly answer questions like these by supporting them with basic information on tools and their potential applications. Along with helping with tool selection for each NC operation, the system stores geometry and cutting data for each tool assembly, makes 3D-tool graphics available for NC and simulation analyses, and saves tool lists from the NC programs for future use. In addition, the recording of cutting data, machining conditions, and best practices permits the optimization of tool use in future applications.
"Features like these are what make TDM such a benefit on repeat jobs," says Smutny, "but it comes into play on new jobs as well. For instance, it might be a different product or application, but maybe the material is the same, so the programmers already know about the behavior of the cutting tools and tool assemblies with this material. Overall we've saved a lot of time and realized increases in accuracy."
Tool presetting was mentioned above, and here, too, TDM's Tool Lifecycle Management brings benefits. TDM works with leading presetter manufacturers to facilitate two-way communication. During the measuring procedure, these systems can access the nominal data for each tool assembly which is stored in the TDM system, and transfer the actual measured data back to TDM to continually fine tune the system. This data transfer is carried out with TDM via DNC or with tool chips. The tools and NC programs simultaneously get to the correct machine, together with the current actual data of the preset tools, and with graphics, photos and/or captions. Wagstaff eventually purchased a presetter to complement TDM, but even if a company doesn't have a presetter it needs to track nominal dimensions so they can know if a tool or tool assembly is suitable for an operation.
The access to accurate data can reduce programming and job setup time, typically by 25%. "We’ve had as many as seven people in the tool crib. Partly due to TDM we now run that area on three,” notes Rasmussen. Smutny adds that, “the company has also grown a lot since we implemented TDM but our programming crew is staffed at roughly the same level as in 2004. We now spend more time preparing revenue-producing jobs and less time searching for information. TDM increased our bandwidth.”
“Keeping track of our approximately 4,000 tool assemblies and the tool components used to be a headache, and consume man hours that can otherwise be used in value-added activities," continues Rasmussen. "Now we know what we need to stock in terms of cutting tools, extensions, holders, collets, you name it, so that's definitely streamlined the purchasing function, in addition to reduction of inventory" he adds. Full knowledge of Wagstaff’s tools and the capabilities of those tools has allowed the company to reduce their purchases in some areas.
He admits that buy-in to the new system wasn't automatic. "People don't like to adopt new things, so there's always some degree of hesitancy. Today, however, the situation is different. One of our programmers recently mentioned to me that he didn't know how he did his job without TDM. It's become a vital part of our successful operation."
About Wagstaff - World Leader in Direct Chill Casting
Founded in 1946, Wagstaff, Inc., a Spokane, Washington based manufacturer, provides machinery, technology, and service to enable aluminum producers to transform molten aluminum into solid shapes – “billets” (rounds) and “ingots” (slabs) using “direct chill” casting. The direct chill casting process uses water to chill molten aluminum in order to solidify it into desired shapes for further processing by sheet, plate, extrusion, rod, and forged part manufacturing. Around the world, aluminum producers look to Wagstaff for the know-how and equipment to safely cast aluminum.
Wagstaff develops, engineers, designs, and manufactures sophisticated molds, casting machines, automated systems, and ancillary equipment at our Spokane and Kentucky facilities and has commissioned systems in 58 countries thus far. With its expansive engineering department and state-of-the-art manufacturing capabilities, Wagstaff provides innovative, comprehensive solutions to aluminum producers for maximum quality and productivity in the casthouse.
In addition to its core aluminum business, Wagstaff has expanded its efforts to the custom machining industry with the Wagstaff Applied Technologies group. They utilize Wagstaff innovation and craftsmanship to provide performance-driven solutions in machining, process automation, and project management. Wagstaff Applied Technologies has experience serving nuclear, defense, semi-conductor, and OEM sectors.