Industry 4.0 for Fong Lee Metal
Since 1981, Fong Lee Metal has been a strong partner for the oil and gas industry as a manufacturer for crucial metal parts such as wellhead housings or tubing hangers that are needed for the extraction and transport of fossil fuels. The Singapore-based company processes special alloys such as 718 Inconel and Super Duplex stainless steel into parts that have very little room for error, requiring high precision engineering. “Quality demands for our products are steep”, emphasizes Pih Yen Loh, Manager Engineering at Fong Lee Metal. “The parts we produce are used in rough environmental conditions and need to last for a long time.”
At the same time, efficiency needs to be on point as well as competitive pressure is rising in Southeast Asia just as much as everywhere else. Early on, Fong Lee CEO Gary Choy decided that digitalization and interconnectivity are key factors both in improving quality and efficiency: “I regularly visit trade fairs in Europe to keep up with global developments in the sector, and I was always impressed by all the Industry 4.0 technology on display there”, he reports. “It was clear to me that this was the path for Fong Lee Metal as well if we wanted to keep our competitive edge.”
Digital Tool Management – Before and After
As a result, Fong Lee Metal made it its mission to streamline its processes and manage them by an ERP System to create full transparency across departments as well as for the customer. For the manufacturing process specifically, a tool management solution was in high demand. “We realized there was quite a bit of variance between the cutting parameters and tool assembly used between different production employees leading to inconsistencies in the quality level of our parts – which is obviously inacceptable, no matter how big or small the inconsistency might be”, says Pih Yen Loh.
The goal then was clear: The processes and tooling needed to be standardized
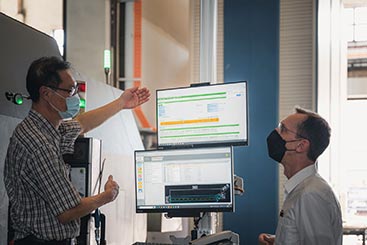
Michael Lee from Tech Konner, a certified TDM Sales & Service Partner, knows the requirements of Fong Lee Metal very well and referred to the solution from TDM Systems. A solution that fits perfectly with the demand for more Industry 4.0. and which Fong Lee Metal also opted for. Tech Konner took over the implementation and is helping the company to further develop its application 4.0. The decision in favor of TDM Systems and Tech Konner is paying off for Fong Lee Metal.
Thanks to the database function of the TDM solution, cutting parameter data can be stored centrally and accessed by all employees – leading to a uniform data status across the entire workforce. And with the added TDM Tool Crib Module, efficiency in internal logistics and tool provision could be significantly improved since for every job, complete tool lists including assembly instructions can be booked. The tool crib module also provides an overview of all tools that are stored or in use, creating full transparency across the shopfloor. Pih Yen Loh emphasizes: “This allowed us to standardize our processes and quality level exactly like we wanted, and the efficiency increase lead to significant reduction in costs.”
Fully integrated: Interfaces for Mastercam and TopSolid’Cam
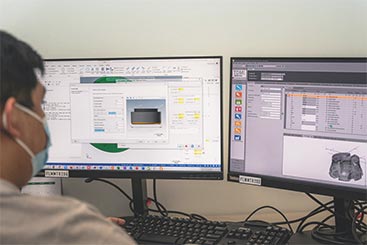
Another big factor for the decision for the TDM Systems solution was its integration capabilities with all relevant CAM systems. Especially the interfaces for Mastercam and TopSolid’Cam were important as both play a big role in the digitalization of the planning processes and shopfloor level at Fong Lee Metal. “This is exactly the integration that we were looking for”, says Pih Yen Loh. “We need everything to work together to create an all-encompassing system that realizes the transparency, efficiency and flexibility potential of Industry 4.0 – and TDM Systems is a huge component in that for us.” And the story will continue: to move on the path of Industry 4.0 Fong Lee Metal is already planning further steps of seamless data flow and integrated processes on the shopfloor level.