"Everything started out very small," recalls Günther Frühschütz, tool management foreman of the GROB factories in Mindelheim. "In 1998 our former factory manager acquired an entry-level version of TDM. The software was tailored to the requirements of small and medium-sized companies. This made it ideal for a test run." At that time, there were still tool cabinets stacked to the ceiling in GROB's factory halls. "In principle, nothing at all was managed back then," says Frühschütz. The machine operators got the tools from the cabinet themselves and put their marker in the empty compartment. This placeholder helped to understand at which machine an item was located. "It was time to convert the system completely; that was a mammoth task that I have only experienced once in the 40 years with the company." The test run was successful. The management of GROB decided to acquire the full version and combine it with the digitally controlled tool crib elevators. "This system – with many expansions and improvements – continues to function as an indispensable cog in the wheel of our production to this day."
Tradition and Internationality
Tool use at the machinery manufacturer GROB is high. Around 25,000 tool assemblies composed of 20,000 items are being used at the Mindelheim plant, the headquarters of the internationally operating family-owned company. Their product portfolio ranges from universal machining centers to highly complex manufacturing systems with their own automation. Their largest customer is the automotive industry. Worldwide, GROB has 4,600 employees, more than 3,300 of them in Mindelheim. Other manufacturing facilities are located in São Paulo in Brazil, Bluffton in the USA and Dalian in the People's Republic of China. GROB has been on a growth course for years. Over the past few years, the production capacity has been expanded by over 35 percent and 900 new jobs have been created in Mindelheim alone.
The Global Tool
This growth and the internationality of the company are also a challenge for tool management. All factories are centrally controlled from Mindelheim. "Our goal", says Georg Wilbiller, System Administrator of Tool Management at GROB, "is to make it possible for the programs run in Germany, including the tools used, to be carried over to Brazil, the USA and China one by one." Wilbiller receives inquiries from sister factories every day. Before a tool assembly is used overseas it is initially tested in Mindelheim to determine if it corresponds to internal specifications. Once released, the factories abroad can all access data stored in Mindelheim.
From Screen to Machine
But back to Mindelheim. The centerpiece of continuous Tool Lifecycle Management at GROB is positioned like an island in the middle of the production hall. Here you will find offices, set-up stations and six-meter-high tool crib elevators right in the center in which thousands of individual items wait to be put together into tool assemblies. The first step in the tool circulation is initially done virtually and in a different department, CNC Programming. Here, new production orders are created in the CAD/CAM system. The programmers access a pool of over 25,000 real available tool assemblies via TDM. The 3D-models are carried over into the CAD/CAM program – at GROB these are Siemens NX 8.5 and TopSolid'Cam 7 – from the TDM-system via an interface.
The Shopfloor under Control
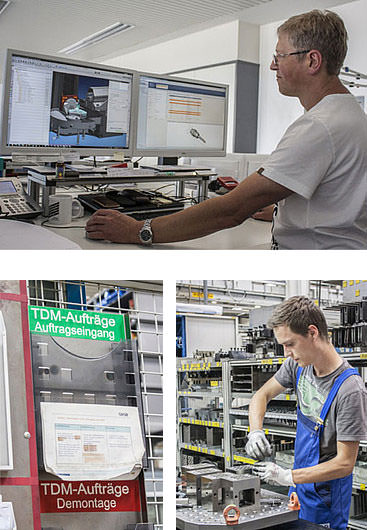
If the order goes to production, it ends up in TDMshopcontrol. The module records the entire tool circulation. "When we started with TDM, we didn't have the TDMshopcontrol module yet," recalls Frühschütz. "In some cases, too many tools were being dismantled and put away again after the end of an order. This ended with TDMshopcontrol, which always compares the new orders with the tool stock at the machine."
The responsible skilled worker still gets the order for the installation as a slip of paper. The digital support begins at the tool crib elevator. The employee opens the TDM order and the storage shelves immediately move forwards. The tool items are removed and written off. If the employee has to switch from one elevator to another, the TDM order also "migrates" to the next screen.
Good Installation is Half the Battle when it Comes to Production
If all items are on the cart, it goes to tool installation. The skilled worker has access to a TDM workspace where things like the design drawing of the tool to be assembled can be seen. If all tools of an order have been assembled, tool presetting follows. Via an interface, the presetting system gets the nominal values from the TDM data base and, after successful measurement, sets the status of the tool assembly to preset. The measurement values then leave the TDM system and go to programming and are converted into machine data. In addition to managing the actual tools, the clamping tools required for an order are also recorded via TDM. GROB has relied on external setup work for over 15 years to take machine setup times away from the machine and to minimize idling to a large extent. The orders are preassembled on a system of pallets and inserted into the machine.
Discontinued Machine Crash Model
Via the TDM Fixture Management Module, the programmer can access 3D-models of all pallet systems and holders and assemble them in the CAM-system. TDM forms the direct interface between the "virtual" programming on the screen and the "real" production on the machine. A huge advantage, as Günther Frühschütz emphasizes: "The programmer can take the data from TDM and make his collision analysis directly. Since introducing this process, our crash rate has declined very sharply."
This not only spares the employees at the machine much trouble, but in particular saves money. Each collision means extensive damage and machine down time – and machine hours are expensive. Instead, the pallet systems planned via TDM and pre-rigged externally allow the machines to simply run and yield what GROB would ultimately like: Added value.