BRUDERER is a family company with a global reputation as an innovator in cutting-edge technology, employing around 460 people worldwide, 370 of them in Frasnacht, Switzerland. It is here that the medium-sized company has been developing and producing its stamping machines – an industry favorite worldwide – for over 75 years. Like all companies in well-developed industrial countries, BRUDERER faces the challenge of keeping its manufacturing costs competitive in the face of high labor costs.
A visionary pioneer
To bring transparency to tool management and free CAM programmers from time-consuming research, BRUDERER decided to introduce digital tool management from TDM Systems exactly 30 years ago. Michael Fankhauser, the system administrator whose responsibilities include the introduction of TDM, has been with the company since 1983 and remembers this well. At that time, the foremen had to order the tools required themselves, which eventually turned into a kind of organized chaos. Since there was a lack of transparency about the existing tools and their data, the NC programming was also time-consuming. In 1991, BRUDERER was one of the first customers in Switzerland to introduce digital tool management from TDM Systems.
Digitalization reduced procurement costs by 30%
BRUDERER spent the equivalent of two man-years recording around 5000 items. This was a huge effort, but one which Fankhauser believes quickly paid off. In a short period of time, procurement costs for resources decreased by around 30 percent thanks to the transparency gained. With available graphics, fewer error occurred during tool assembly. Most importantly, it was a win for the CAM programmers: It now took them less time to create the programs.
TDM – the most important software used in production after ERP
For a good 20 years, BRUDERER used the TDM solution to manage their tools. However, with the expansion of the tool management solution ten years ago, the Swiss company also wanted to exploit the potential of the tool data more extensively and, according to Fankhauser, with the upgrade to TDM V4 in 2011 "a new dynamic came into play". BRUDERER gradually introduced new modules and interfaces. This decision made TDM the most important software used today by the Swiss firm for its production, after the ERP system. "Without TDM, no tools can be used on integrated machines, and no orders can be processed," explains Fankhauser.
Future machine integration project
"We want the most secure processes possible, and that also always means avoiding manual transmission," explains Fankhauser. The goal of the dedicated BRUDERER team was a consistent data connection from TDM to the machines. This may sound simple but, in practice, the project took clever planning and a corresponding amount of effort. At present, there is no general solution. Not to mention the fact that only a few machine manufacturers or machine control developers allow bidirectional data transfer via an internal interface. The development of an interface for the machine control system in order to transmit comprehensive tool data was therefore a challenge. As Fankhauser points out, it depends on a wide range of factors, such as the type of machine or the control software used.
Realizing the potential for optimization
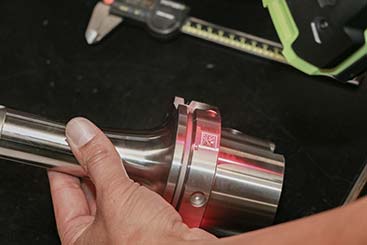
Since the BRUDERER team expected significant potential for optimization from machine integration, they opted for the project. Just as in 1991, they were pioneers once more – and not just in their industry. The developers needed a whole year to be able to transfer the various tool data from TDM to the machine control systems used at BRUDERER. To complete this task, TDM Systems brought in a development partner, the company ECI. The so-called "ECI Box" is a type of middleware, which takes over the data exchange between TDM and the machine control system.
Bidirectional data communication with the machine
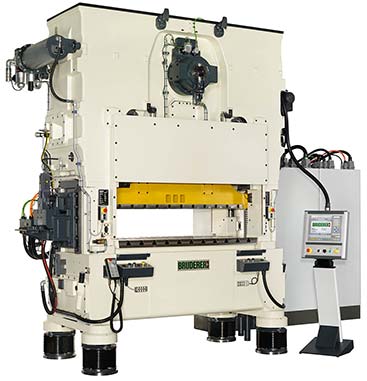
As Fankhauser explains, the machine integration that was implemented is an extension of the TDM Shopfloor Manager module. This allows the real machine stocks and tool conditions to be taken into account in parallel with the planning of tool requirements and the provision of the necessary tools. An example: The ECI interface is used to transfer the actual service lives of the tools used to the TDM database. This key factor for process reliability had previously been planned and operated on the basis of values taken from past experience and assumptions. These are now constantly being verified with actual data from the machine. That is why the tools are now longer in use than before.
Reduced setup effort thanks to service life monitoring
Another advantage: A so-called traffic light system signals to the machine operator when the service life of the tools being used falls within a critical range. As a result, they can now plan ahead and ensure that the tool they need will be available when the tool comes to the end of its life. The setup effort has also been reduced. As the tool stock is clearly shown on the machine, only the additional tools required for each order need to be assembled. All these points help BRUDERER to get even more mileage from their machines.
Fewer faults and machine downtimes
All the tool data required for production is sent directly to the production machine from TDM, without any manual data input whatsoever. To activate the data transfer, the machine operators only have to scan the data matrix code on the tool and then place it in the assigned magazine location on the machine. According to Fankhauser, this optimized process "now prevents transmission errors". BRUDERER is still in an extended test phase, which is designed to collect and analyze data. However, initial evaluations indicate that the interface guarantees significantly higher process reliability. "Since the data has been automatically transferred to the production machines, no processing errors or collisions have occurred due to incorrect tool data," underlines Müller.
The cornerstone for further digital development
It is also very important that during data input the machines at BRUDERER are no longer standing still. Before the introduction of the interface, it was not possible to manufacture using certain machine controls whilst manually transferring data. With several set-up processes each day, these machine downtimes proved quite significant when added together. For Fankhauser, one thing is very clear: "The integration of our production machines into the TDM solution has definitely been worthwhile." This is not just because it allows for more efficient production. It has also laid the foundation for the further digital development of how production is organized at BRUDERER. In addition, the solution relieves the machine operators of routine work that has to be done manually and, as Müller emphasizes, "last, but not least, makes our workstations on the shopfloor more attractive".
BRUDERER's objectives
- Fully secure processes on the shopfloor
- Avoiding manual data input on the machine
- Consistent data connection to the machine
- Realizing the machine's potential for optimization
Process innovation through machine integration
- Automated tool data transfer to the machine control activated by the data matrix code on the tool
- Bidirectional data connection to the machine
- Comprehensively transparent and efficient tool preparation taking account of:
- tool conditions and machine stocks
- tool requirements for each NC order and
- continuously monitored tool lives via the traffic light system
- Continuous verification of the NC plan data by securing the data feedback from the machine