Zunächst einige Hintergrundinformationen: Wagstaff ist ein wichtiger Akteur in der Aluminiumindustrie und führend in der Entwicklung und Herstellung von Systemen und Ausrüstungen, die zur Herstellung von Primäraluminiummasseln und -barren im Direktkokillenguss benötigt werden. Ihr Werk in Spokane misst 12.500 qm und umfasst die Bereiche Forschung und Entwicklung, Fertigung, spanabhebende Bearbeitung, Montage, Prüfung und Versand. Das Unternehmen verfügt über ca. 30 CNC-gesteuerte und 20 herkömmliche Maschinen.
Dies alles ist aber nicht über Nacht entstanden. Die amerikanische Erfolgsgeschichte begann 1946 in einem Pumpengebäude hinter dem Wohnhaus von George Wagstaff. Im ersten Jahr benutzte der gelernte Mechaniker Wagstaff eine Drehbank aus überzähligen Rüstungsbeständen, um Zulieferteile für eine Maschinenfabrik herzustellen. Tagsüber arbeitete er an der Drehbank und nachts im Aluminiumwerk Kaiser Trentwood. Im Laufe der Zeit zahlte sich seine harte Arbeit aus. Er konnte eine zweite Drehmaschine erwerben und erweiterte damit seinen Betrieb. Seitdem expandiert das Familienunternehmen kontinuierlich. Mit Beginn der 1960er Jahre wurde es unter der Leitung von Georges Sohn Bill Wagstaff zum anerkannten Marktführer im Bereich Direktkokillenguss von Aluminium.
Heute wird Wagstaff von den Nachkommen von George Wagstaff geführt. Firmenchefin ist seine Enkelin Barbara (Wagstaff) Parkes. Wagstaff ist mit Niederlassungen rund um den Globus vertreten und hat über 300 Kunden in 58 Ländern.
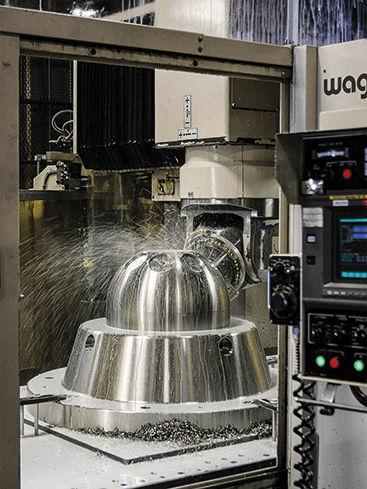
„Ein wachsendes Unternehmen steht auch vor vielen Herausforderungen“, erläutert Jeff Smutny, Leiter der Fertigungstechnik bei Wagstaff. „An einem bestimmten Punkt, so um das Jahr 2004, wurde uns klar, wie viel Geld wir für verlorene Informationen ausgeben. Informationen wurden in Prozessdokumenten für bestimmte Produktlinien gespeichert, viele lagen auch in unserem CAM-System und andere in Excel-Tabellen. Es war schwierig, diese Informationen im Auge zu behalten und für neue Aufträge zu nutzen. Diese Vorgehensweise war nicht sehr effizient, und jeder hatte anscheinend ein etwas anderes Verständnis davon, wie bestimmte Werkzeuge verwendet werden sollen. Das hat uns Zeit und Geld gekostet.“
Russ Rasmussen, Fertigungstechniker bei Wagstaff, erinnert sich gut daran. „Jeder hatte seine eigene Art und Weise, mit den Informationen umzugehen, und es gab zahlreiche Orte, an denen sie aufbewahrt wurden. Die Informationen wurden nicht unbedingt zwischen verschiedenen Anwendern ausgetauscht“, fügt Rasmussen hinzu. „Der Informationsaustausch zwischen NC-Programmierung und Fertigung war beispielsweise oft nicht zufriedenstellend. Wir hatten keine Datenbank für Stammdaten, so dass ständig Änderungen, Klone und Mutationen entstanden. Die Leute arbeiteten mit Informationen aus zweiter Hand und bedienten sich nicht an der Quelle.“
Dies machte es sehr schwierig, wichtige Vorgänge wie das Simulieren eines Bauteilprogramms durchzuführen und dabei zu wissen, dass man mit aktuellen, korrekten Informationen arbeitet.
Erforderliche Daten

Diese Situation begann sich 2005 zu ändern, als Smutny als Gast von Walter und dem örtlichen Walter Vertriebspartner den Walter Hauptsitz in Deutschland besuchte. Smutny lernte bei Walter das Tool Lifecycle Management-System von TDM System kennen, das dort eingesetzt wird und war von seinem Umfang und seinen Fähigkeiten beeindruckt. „Unsere Mitarbeiter haben schon seit einiger Zeit über Werkzeugvoreinstellgeräte nachgedacht, aber das Datenmanagement reichte uns nicht aus“, erinnert sich Smutny. „Nachdem wir das TDM-System in Betrieb gesehen hatten, war klar, dass wir ein Werkzeugverwaltungssystem brauchen, bevor wir ein Voreinstellgerät einsetzen.“ Außerdem stellte er fest, dass das Walter TDM über Schnittstellen zum gleichen CAD-System und dem gleichen Bauteilprogramm-Verifikationssystem verfügte, das auch bei Wagstaff zum Einsatz kam.
„Unser Tool Lifecycle Management sorgt dafür, dass die Werkzeugdaten dort verfügbar sind, wo sie gebraucht werden und wann sie gebraucht werden“, erklärt Dan Speidel, Vertriebsleiter bei TDM Systems Inc. „Es verbindet CAM-Systeme, Voreinstell- und Lagersysteme sowie CNC-Maschinensteuerungen, kann aber auf der Planungs- und Ausführungsebene, beispielsweise bei PPS-, ERP- und MES-Systemen, vorgeschaltet werden. Ein Tool Lifecycle Management-System, das einen so breiten Bereich abdecken soll, muss offen sein und zahlreiche Import- und Exportschnittstellen bereitstellen. Es muss Daten aus verschiedenen Quellen, beispielsweise aus Herstellerkatalogen oder selbst erstellten 3D-Modellen, in eine zentrale Datenbank integrieren können.“
Speidel fügt hinzu, dass das System Daten aus der Produktion sammelt und an andere Systeme überträgt. Das Tool Lifecycle Management beeinflusst den gesamten Prozess von der Auswahl der Werkzeuge über deren Einsatz in der Produktionsplanung bis hin zum nahtlosen Transfer und Einsatz in der Fertigung. Die Informationen aus den einzelnen Prozessschritten fließen kontinuierlich in eine zentrale Datenbank zurück, so dass eine wachsende Datenmenge entsteht, auf die im gesamten vernetzten System zugegriffen werden kann. Das war genau das System, das gebraucht wurde.
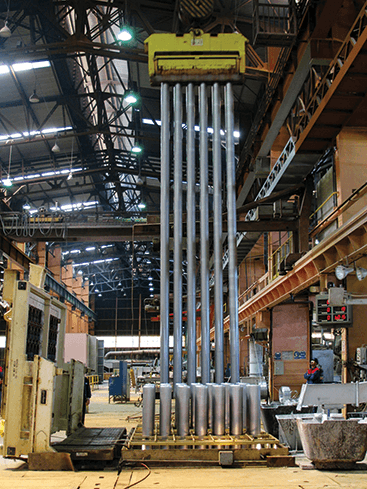
„Wagstaff hatte die typischen isolierten Informationsinseln, die wir in so vielen Unternehmen sehen“, erläutert Speidel. Die alte Vorgehensweise war, einen Produktionsauftrag zu bekommen, ihn an die Fertigungsplanung zu übergeben, um den Fertigungsprozess zu entwerfen und zu planen und ihn dann an die NC-Programmierung weiterzugeben. Sobald das NC Programm fertig war, gingen sie mit dem Programm zum Werkzeuglager und suchten nach dem Werkzeug für den Auftrag. Dabei musste häufig das ganze Lager durchsucht werden und der Maschinenbediener musste dann oft noch sein eigenes Lager ebenfalls durchsehen. Natürlich hat jeder auch seine eigenen Vorlieben für Werkzeuge.“ Das war weder einheitlich noch effizient.
„Die Fertigung hatte zahlreiche Werkzeugregale an verschiedenen Orten, aber es gab keine Möglichkeit, alle Werkzeuge digital zu suchen, so dass die Mitarbeiter herumlaufen und suchen mussten. Das zentrale Werkzeuglager schärfte in erster Linie Werkzeuge nach und versuchte, die Mindestlagerbestände aufrechtzuerhalten“, fährt Rasmussen fort.
„Sie hatten überall Werkzeugdaten“, ergänzt Speidel. „In Excel-Tabellen, Word-Werkzeuglisten, Werkzeuglagerkarten, in Notepad-Anwendungen auf persönlichen Laufwerken, auf Laufzetteln, in Werkzeugbüchern an den Maschinen oder einfach im Kopf. Der entscheidende Punkt ist, dass es kein zentrales Werkzeugsystem gab und diese Informationen nicht digital nachvollziehbar oder durchsuchbar waren. Sie nutzen auch Vericut von CGTech, um die Werkzeugbahn zu simulieren, aber die Werkzeuginformationen in diesem System waren nicht vollständig in das CAM-System integriert.“
Obwohl die Kritik berechtigt ist, sollte berücksichtigt werden, dass sich viele Unternehmen in dieser Lage befinden. Die Wagstaff Mitarbeiter Jeff, Russ und Howard Estes (jetzt im Ruhestand) waren jedoch entschlossen, etwas dagegen zu unternehmen. Sie erkannten, dass sie sich in Bezug auf ihre Werkzeuginformationen besser organisieren mussten. Dabei ging es auch darum, das über Jahrzehnte hinweg bei der Herstellung hochtechnisierter Produkte aufgebaute umfangreiche Spezialwissen weiterhin nutzen zu können.
Tool Lifecycle Management
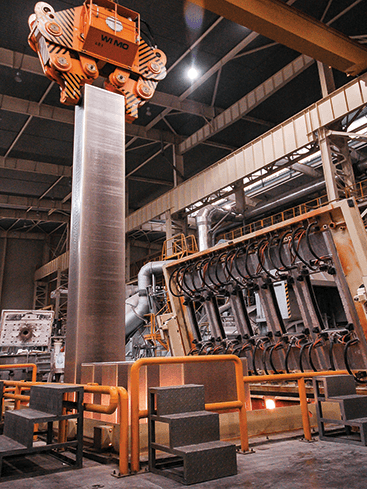
Die Neuorganisation begann mit der eigentlichen Definition der Werkzeuge, dem ersten Schritt im Tool Lifecycle Management. Das war für Wagstaff keine leichte Aufgabe, denn „wir haben rund 4.000 Werkzeugbaugruppen und viele, viele weitere Werkzeugkomponenten“, beschreibt Rasmussen die Situation.
Speidel fügt an, dass sich Unternehmen oft mit den generischen Komplettwerkzeuge des CAM-Systems begnügen, aber dafür einen hohen Preis zahlen. „Wie oft haben Sie gesehen, wie Programmierer ihren Schreibtisch verlassen und in die Fertigung gehen, um nach dem richtigen Werkzeug zu suchen? Oder sie gehen zum Werkzeuglager, um zu fragen: haben wir so etwas wie das hier? Wenn Ihre NC-Programmierer nicht in der Access-Datenbank nach Informationen über den Inhalt des Werkzeuglagers suchen können, müssen sie ihren Arbeitsplatz verlassen und nach den entsprechenden Werkzeugen suchen.“ Das Ergebnis: Zeitverlust.
Die Verwendung der eigentlichen Werkzeuggrafik anstelle der generischen Werkzeugmodelle erspart das Rätselraten und beseitigt die Unsicherheit bei der Werkzeugerstellung. Durch die gezielte Identifizierung der einzelnen Werkzeuge und Komponenten kann eine effiziente und wiederholbare Genauigkeit erreicht werden.
Bei der Werkzeugauswahl stellen sich weitere Fragen, beispielsweise welche Werkzeuge für welche Prozessschritte am besten geeignet sind. Welche Kombinationen sind effizient? Das Tool Lifecycle Management von TDM hilft Wagstaff, solche Fragen schnell zu beantworten, indem es grundlegende Informationen über Werkzeuge und deren Einsatzmöglichkeiten bereitstellt. Neben der Hilfestellung bei der Werkzeugauswahl für jede NC-Operation speichert das System Geometrie- und Schnittdaten für jedes Komplettwerkzeug, stellt 3D-Werkzeuggrafiken für NC- und Simulationsanalysen zur Verfügung und speichert für die spätere Verwendung Werkzeuglisten aus den NC-Programmen. Darüber hinaus ermöglicht die Erfassung von Schnittdaten, Bearbeitungsbedingungen und bewährten Vorgehensweisen die Optimierung des Werkzeugeinsatzes in zukünftigen Anwendungen.
„Diese TDM-Funktionen sorgen für große Vorteile bei Wiederholaufträgen“, erläutert Smutny. „Aber sie helfen auch bei neuen Aufträgen. Es könnte sich beispielsweise um ein anderes Bauteil oder eine andere Anwendung mit dem gleichen Material handeln, so dass die Programmierer bereits über das Verhalten der Werkzeuge und Komplettwerkzeuge mit diesem Material Bescheid wissen. Zusammengefasst haben wir viel Zeit gespart und die Genauigkeit erhöht.“
Auch bei der oben erwähnten Werkzeugvoreinstellung lassen sich mit dem Lifecycle Management von TDM Vorteile erzielen. TDM arbeitet mit führenden Herstellern von Voreinstellgeräten zusammen, um die Kommunikation in beide Richtungen zu erleichtern. Während des Messvorgangs können diese Systeme auf die Solldaten jedes im TDM-System gespeicherten Komplettwerkerkzeug zugreifen und die gemessenen Istdaten an TDM zurückübertragen, um damit kontinuierlich die Qualität des Systems zu verbessern. Diese Datenübertragung erfolgt mit TDM über DNC oder mit Werkzeugchips. Die Werkzeuge und NC-Programme kommen gleichzeitig an der richtigen Maschine an, zusammen mit den aktuellen Ist-Daten der voreingestellten Werkzeuge und mit Grafiken, Fotos und/oder Beschriftungen. Wagstaff kaufte schließlich zur Ergänzung des TDM-Systems ein Voreinstellgerät. Auch wenn ein Unternehmen über keinen Voreinsteller verfügt, muss es dennoch die Sollmaße verfolgen, um entscheiden zu können, ob ein Werkzeug oder ein Komplettwerkzeug für eine Anwendung geeignet ist.
Der Zugriff auf genaue Daten kann die Programmier- und Rüstzeiten üblicherweise um 25 % reduzieren. „Wir hatten bis zu sieben Mitarbeiter im Werkzeuglager beschäftigt. Teilweise durch TDM bedingt, haben wir das nun auf drei Mitarbeiter reduziert“, erläutert Rasmussen. Smutny fügt hinzu: „Das Unternehmen ist seit der Einführung von TDM ebenfalls stark gewachsen, aber unser Programmierer Team hat noch die gleiche Personalstärke wie 2004. Wir verbringen jetzt mehr Zeit damit, umsatzbringende Aufträge vorzubereiten und weniger Zeit mit der Suche nach Informationen. TDM hat unsere Bandbreite erhöht.“
„Die Verfolgung unserer ca. 4.000 Werkzeugbaugruppen und der Komplettwerkzeuge war früher ein großes Problem und verschlingt viele Arbeitsstunden, die besser für wertschöpfende Tätigkeiten genutzt werden können“, ergänzt Rasmussen. „Jetzt wissen wir, was wir in Bezug auf Schneidwerkzeuge, Verlängerungen, Halter oder Spannzangen im Lager haben müssen. Damit wird die Einkaufsfunktion definitiv gestrafft, zusätzlich zur Reduzierung des Lagerbestands“, fügt er hinzu. Umfassende Kenntnisse über die Wagstaff Werkzeuge und die Einsatzmöglichkeiten dieser Werkzeuge haben es dem Unternehmen ermöglicht, das Einkaufsvolumen in einigen Bereichen zu reduzieren.
Er räumt ein, dass der Einstieg in das neue System nicht problemlos war. „Die Leute nehmen nicht gerne neue Dinge an, deshalb muss man immer mit einem gewissen Widerstand rechnen. Heute ist die Situation jedoch anders. Einer unserer Programmierer hat mir kürzlich gesagt, dass er sich gar nicht mehr vorstellen kann, seinen Job ohne TDM zu erledigen. TDM ist damit zu einem wichtigen Bestandteil unserer erfolgreichen Arbeit geworden.“
Quellenangabe
Adaption des Anwenderberichts mit freundlicher Genehmigung von Modern Machine Shop Magazine.
Wagstaff - Weltmarktführer im direkten Kokillengussverfahren
Das 1946 gegründete Unternehmen Wagstaff, Inc. mit Sitz in Spokane (Washington) bietet Maschinen, Technologien und Serviceleistungen an, mit denen Aluminiumproduzenten geschmolzenes Aluminium im direkten Kokillengussverfahren in feste Formen (Barren, Pressbolzen) gießen können. Beim Kokillengussverfahren wird geschmolzenes Aluminium mit Wasser gekühlt, um es in den gewünschten Formen erstarren zu lassen und für die Weiterverarbeitung in der Blech-, Platten-, Strangpress-, Stab- und Schmiedeteilfertigung zu verarbeiten. Weltweit vertrauen Aluminiumproduzenten Wagstaff, wenn es um das Know-how und die Ausrüstung zum sicheren Gießen von Aluminium geht.
Wagstaff entwickelt, konstruiert und fertigt an den Standorten Spokane und Kentucky anspruchsvolle Formen, Gießmaschinen, automatische Systeme und Zusatzeinrichtungen und hat bisher Anlagen in 58 Länder geliefert. Wagstaff bietet Aluminiumproduzenten mit seiner umfangreichen Konstruktionsabteilung und modernsten Fertigungskapazitäten innovative, umfassende Lösungen für höchste Qualität und Produktivität in der Gießerei.
Neben dem Aluminium-Kerngeschäft hat Wagstaff mit der Wagstaff Applied Technologies Gruppe seine Aktivitäten auf den Sondermaschinenbau ausgeweitet. Mit der Innovationskraft und dem handwerklichen Können von Wagstaff können leistungsorientierte Lösungen in den Bereichen Zerspanung, Prozessautomatisierung und Projektmanagement angeboten werden. Wagstaff Applied Technologies hat Erfahrung im Nuklear-, Verteidigungs-, Halbleiter- und OEM-Bereich.