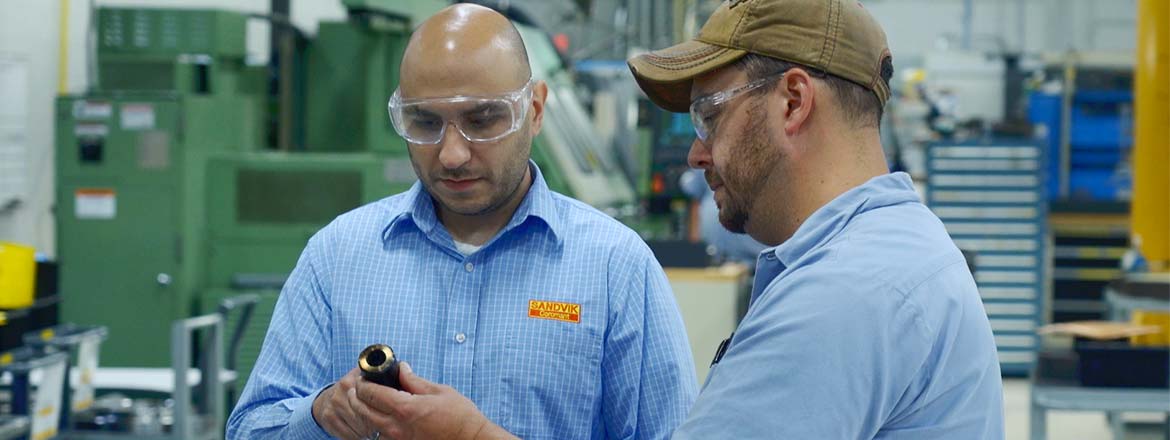
Die Verbesserung des Prozess- und Datenmanagements ist der Schlüssel zur Steuerung effizienter Produktionsanlagen.
Wenn Sie zu einem der größten und renommiertesten Werkzeughersteller der Welt gehören, reicht es nicht aus, nur gute Technologie einzusetzen. Sandvik Coromant suchte nach besseren Verfahren, um Werkzeuge zu verfolgen, zu verwalten und die Produktion zu optimieren. „Ein effizientes Kostenmanagement, die Bereitstellung wichtiger Daten und die Prozessoptimierung sind für ein Unternehmen wie Sandvik Coromant von entscheidender Bedeutung“, erklärt Julio Vasconcelos, Engineering Manager im Werk Mebane von Sandvik Coromant. „Wir setzen auf digitale Lösungen, eine schlanke Fertigung und Effizienz.“
Sandvik Coromant Mebane produziert hauptsächlich rotierende Standardwerkzeuge (Fräser und Bohrer), aber auch einige Sonderwerkzeuge werden dort hergestellt. Das Unternehmen verwaltet auch die Daten bereits hergestellter und ausgelieferter Werkzeuge. Bei der Werkzeugherstellung kommen über 2.000 Komplettwerkzeuge (Werkzeuge, Spannzangen, Halter) zum Einsatz, wobei diese digital verwaltet werden in TDM.
Bessere Steuerung der Werkzeuge an der Maschine
Vasconcelos war bewusst, dass damit enorme Datenmengen entstehen. Den Überblick über diese Daten zu behalten, wurde zu einem immer größer werdenden Problem. „Es wurde deutlich, dass wir einen besseren Weg benötigen, um diesen wachsenden Datenberg zu bewältigen, und dass wir die Werkzeuge an der Maschine steuern müssen“, stellt Vasconcelos fest. „Wir mussten eine Lösung entwickeln, die auf unsere schlanken Fertigungsverfahren abgestimmt ist. In der Vergangenheit hatte jeder Fertigungsingenieur seine eigene Methode entwickelt, die Werkzeuge zu planen, die Daten auszuwerten und den Maschinenbedienern bereit zu stellen. Wir suchten nach einer besseren Lösung.“
Verloren gegangene Daten verursachten enorme Kosten
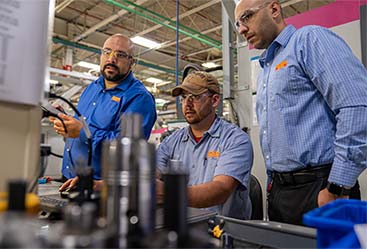
„Durch die Maschinenstillstände, die natürlich mit zusätzlichen Kosten verbunden sind, haben wir zu einem bestimmten Zeitpunkt erkannt, wie viel Geld wir für verloren gegangene Daten ausgeben. Es gab Daten, die in Prozessdokumenten für bestimmte Produktlinien festgehalten wurden, Daten, die sich in unserem CAM-System befanden und Daten, die nur in Excel-Tabellen vorhanden waren. Den Überblick über diese Daten zu behalten, war schwierig. Das Verfahren war einfach nicht effizient. Es war eine Herausforderung für unsere Mitarbeiter, sich daran zu erinnern, an welcher Stelle Daten abgelegt werden sollen, und jeder schien etwas andere Ansichten darüber zu haben, wie bestimmte Werkzeuge verwendet werden sollen. Das war auch eine Situation, die uns Zeit und Geld gekostet hat.“
Leandro Pereira, Automatisierungsingenieur bei Sandvik Coromant Mebane, erinnert sich gut daran. „Jeder hatte seine eigene Art und Weise, mit den Daten umzugehen, und es gab zahlreiche Orte, an denen sie aufbewahrt wurden. Am schwerwiegendsten war sicherlich die Tatsache, dass die Daten in vielen Fällen nicht zwischen verschiedenen Nutzern ausgetauscht wurden.“
TDM bietet vielversprechende Möglichkeiten zur Verwaltung von Werkzeugdaten an
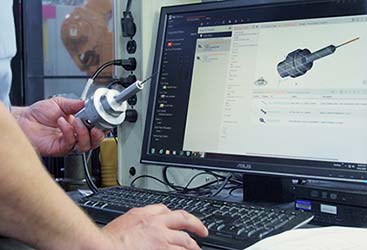
Sandvik Coromant gehört zum globalen Industriekonzern Sandvik, der seit geraumer Zeit Lösungen für die Automatisierungstechnik und zukunftsweisende Fertigungsverfahren entwickelt. Vor sechs Jahren führte Sandvik eine umfangreiche Studie über das Werkzeugmanagement durch und stellte fest, dass die Tool Data Management-Software von TDM Systems die beste Wahl für die Kontrolle und Optimierung von Werkzeugdaten ist und daher Teil dieses Szenarios sein sollte. „Da wir wussten, dass die Tool Lifecycle Management-Software von TDM bereits umfassend von Sandvik getestet und evaluiert wurde, bestand kein Zweifel daran, dass dies die richtige Lösung für Sandvik Coromant war“, berichtet Vasconcelos. „Wir haben erkannt, dass TDM in der Lage sein würde, die verschiedenen Systeme, die hier zum Einsatz kommen, zu integrieren.“
Werkzeugdatenmanagement als Garant für den Produktionserfolg
„Das Tool Lifecycle Management sorgt dafür, dass die Werkzeugdaten rechtzeitig dort verfügbar sind, wo sie gebraucht werden“, erklärt Robert Auer, Director of Business Development N.A. bei TDM Systems. „Es verbindet CAM-Systeme, Voreinstell- und Lagersysteme sowie CNC-Maschinensteuerungen, kann jedoch auch auf der Planungs- und Ausführungsebene, beispielsweise bei PPS-, ERP- und MES-Systemen, vorgeschaltet werden.
Viele Unternehmen arbeiten abteilungsübergreifend mit eigenständigen Informationen“, fährt Auer fort. „Die alte Vorgehensweise war, einen Fertigungsauftrag zu bekommen, ihn an die Fertigungsplanung weiterzureichen, um den Fertigungsprozess auszuarbeiten und zu planen und ihn dann an die NC-Programmierung zu übergeben. Sobald das NC-Programm erstellt war, brachten sie es in die Fertigung und suchten nach dem Werkzeug für den Auftrag. Der Maschinenbediener musste dann prüfen, ob ihm die Werkzeuge zur Verfügung stehen, die er für die Herstellung des Werkstücks benötigt, basierend auf seiner Präferenz für einzelne Werkzeuge.
Üblicherweise sind Werkzeugdaten überall in einem Unternehmen zu finden“, stellt Auer fest. „Der entscheidende Punkt ist, dass es kein zentrales Werkzeugsystem gibt und diese Daten nicht digital nachvollziehbar oder durchsuchbar waren.“
Mit Werkzeugdatenmanagement zum Erfolg
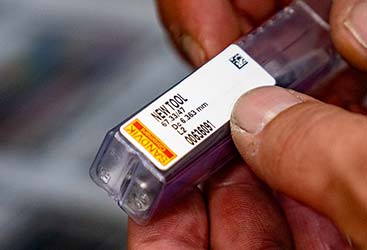
Die Neuorganisation begann mit der eigentlichen Definition der Werkzeuge, dem ersten Schritt im Tool Lifecycle Management. Für die Produktionsstätte Mebane mit ihren Tausenden von Werkzeugen und Komplettwerkzeugen war dies keine leichte Aufgabe.
„Durch den Einsatz von TDM-Werkzeuggrafiken und TDM-Modulen für die Betriebsmittelverwaltung entfällt das Rätselraten und die Unsicherheit bei der Werkzeugerstellung“, erklärt Vasconcelos. „Die TDM-Software ermöglicht die Verwaltung der Werkzeugdaten von der CAM-Software über die Simulation bis hin zur Maschine und zum Bediener.
Wir benötigten ein Simulationssystem, das Datenaus CAM-Systemen und schließlich an den Werkzeugmaschinenbediener übermittelte. Aus der TDM-Umgebung exportieren wir Dateien in unser Simulationsprogramm. Jetzt kann der Programmierer den von ihm verwendeten Werkzeugen vertrauen und sicher sein, dass das, was von der Simulation an den Bediener weitergegeben wird, korrekt ist.
Wir können diese umfassenden Daten überall verwenden. Wir müssen nicht unbedingt ein Werkzeug wechseln, wenn ein neues Produkt beauftragt wird. Damit sparen wir Zeit und Geld“, fährt Vasconcelos fort. „Und das System kann den Werkzeugbedarf kalkulieren, so dass wir nur die benötigten Komplettwerkzeuge auf der Maschine (Halter, Spannzangen, Werkzeuge) vorhalten müssen. Dies spart auch Platz.“
Durch den Einsatz von TDM lässt sich die Produktivität in jedem Werk steigern
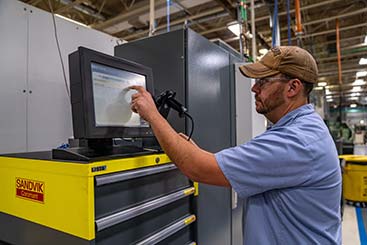
„Den Überblick über mehrere tausend Werkzeuge und Werkzeugkomponenten zu behalten, war früher ein Problem, das nur mit vielen zusätzlich Arbeitsstunden zu lösen war“, fährt Vasconcelos fort. „Jetzt wissen wir, wie wir die Lagerhaltung bei Komponenten, Komplettwerkzeugen etc. organisieren müssen und konnten damit auch den Einkauf optimieren“, fügt er hinzu. Ein weiterer Vorteil war die Reduzierung der Lagerhaltungskosten. Es steht ein umfassendes Wissen über die Werkzeuge und die Einsatzmöglichkeit dieser Werkzeuge zur Verfügung, mit dem in einigen Bereichen die Beschaffungskosten reduziert werden konnten.
Zusammenfassend stellt Vasconcelos fest: „TDM ist zu einem elementaren Bestandteil unseres erfolgreichen Betriebs und zu einem wichtigen Element unserer Zukunftsvision geworden.“ Und wie sieht diese Vision aus? „Wir sehen uns nicht nur als eine fortschrittliche Werkzeugfabrik, wir wollen die Besten sein.“